三种中频对靶磁控溅射类金刚石膜的性能比较
2017-07-24
由于具有不同硬度、密度和从导电至绝缘的传导率,磁控溅射无氢DLC(类金刚石)薄膜具有优异的摩擦学性能,如:高硬度、低摩擦系数、低磨损率和化学稳定性,是一种有广泛应用前景的耐磨损保护薄膜。无氢碳膜的性能强烈依赖于其沉积条件。由于起弧能够引起靶面中毒并导致沉积薄膜的缺陷,靶面起弧是连续DC反应溅射电介质薄膜过程中遇到的主要问题。近来研究表明,利用中频(20—100kHz)磁控溅射可以有效地降低靶起弧频率,显著地改变沉积过程中等离子体的特性,如增加处于脉冲辉光放电中待沉积工件附近的等离子体密度和二次电子温度。还有,以质谱仪分析在非对称双极脉冲DC磁控溅射中工件上离子能量分布过程中发现,特定能量的离子流性能和靶电压波形或特定相位密切相关。尽管有许多通过调节反应溅射中脉冲参数抑止起弧和靶面中毒的论文报道,而就真正和等离子体特性密切相关的双极脉冲中靶电压波形及详细描述其对薄膜结构和性能影响程度的论文很少见到,对于DLC膜的几乎没有。在本次研究中,通过利用带有三种不同模式(即连续DC、脉冲Dc和脉冲AC)的新型中频磁控电源合成了一系列含铬DLC膜,发现三种不同模式下含铬DLC膜性能存在差异,籍此尝试寻找靶电压波形和DLC性能之间的关系。
1.试验部分
利用非平衡磁控溅射方法合成含铬无氢DLC薄膜。在圆柱形真空室中放置了四对磁控对靶,其中包括两个铬靶和六个石墨靶。每对磁控对靶的两个平面磁控靶在真空室中以70cm间隔面对面地排列。工件架置于真空室中心区域。采用规格为420mm×80mm和纯度为99.99%的六个石墨靶和两个铬靶,沉积Cr附着层、CxCry过渡层和DLC表面层。利用偏压电源控制基体负偏压和通向基体的偏流。每个工序的工艺参数可以通过PLC(可编程控制器)进行自动控制。
每个电源带动一对磁控对靶,电源三种可选择工作模式波形和系统示意图示于图1。如图la所示,采用恒流方式的电源具有三种可选择的连接模式,连续DC、脉冲DC和脉冲AC。
在每半个脉冲周期中。磁控对靶中的一个处于负电位的磁控靶作为溅射阴极,如MagA,而另—个磁控靶作为阳极,如MagB。磁控靶电压在另半个周期中方向转换。瞬间阴极生成的二次电子在电场作用下加速向阳极移动,并中和在阳极表面积累的正电荷。非对称双极脉冲DC模式的波形示意图示于图1b。在这种情况下,在固定的“占位”期间,磁控靶在正常工作电压(正常范围为-400v至-600V)下进行溅射。占位时间可以进行设置,使在靶中毒(电荷积累过多)区域的电荷释放不至于引起击穿和起弧。由于磁控靶电位在下半个周期中转变成为相对正值,积累负电荷在“空位”期间通过等离子体进行释放。由于电子质量比相应离子质量小很多,在等离子体中的电子移动速度要比离子移动速度快很多,在空位期间靶电压反向成为正常占位电压的10%,电源的空位时间为12.5us(即整个脉冲周期的50%)。连续DC模式的波形示于图lc,磁控靶A和B的电压是相同的正弦波形,且磁控靶A和B的相位差是半个周期。双极脉冲AC模式的波形示于图1d,和图1c类似,磁控靶A和B的电压是相同的双极脉冲正弦波形,且磁控靶A和B的相位差是半个周期。
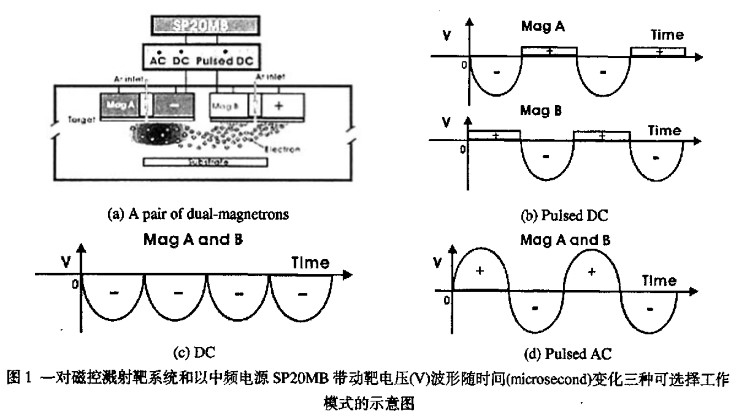
基材采用M2高速钢试样。钢试样表面预先抛光至镜面,平均表面粗糙度为Ra0.08um。镀膜前,将所有试样装入丙酮容器中超声波清洗20min,清洗之后的试样以干燥氮气吹干。以分子泵将真空室抽至3.0x10的-3Pa之后,在-600V偏压和通入氩气至3.0Pa条件下轰击15min。为了衡量三种模式对含铬DLC膜性能的影响,沉积步骤和参数基本上相同。工件加热至之后100摄氏度,通人氩气,沉积压力保持在0.3Pa。主要沉积过程包括三个步骤;1)Cr附着层:启动两个Cr靶在工件表面上沉积厚度约为0.2um的Cr附着层。2)CrxCy过渡层:在氩气条件下,利用两个Cr靶和六个C靶共溅射在Cr附着层上沉积厚度约为1um的CrxCy层,其中Cr靶功率从高逐步降低,C靶功率从低向高递增。3)DLC表面层:利用六个c靶溅射在Cr过渡层上沉积厚度约为1um的DLC表面层。
利用SEM(扫描电子显微镜)分析DLC膜的表面形貌。利用轮廓仪测量薄膜的表面粗糙度。利用纳米硬度计测量合成薄膜的维式硬度。利用划痕仪测量钢基体和DLC薄膜之间的结合力:初始载荷3N、加载速率100N/min和划痕速度10mm/min。利用球一盘试验机考察薄膜的摩擦性能:DLC膜试样粘在盘上,对偶球为Al2O3球:大气环境,负载为5N;转速恒定为1000r/min,相当于线速度0.6m/s。利用带有数码相机目镜的光学显微镜观测磨痕形貌。
2.结果和讨论
试验结果表明,利用脉冲磁控靶电压可提高等离子体中的离子流和离子能量。通过振荡电磁场形成等离子体的活性要比DC等离子体的要高(也就是说,具有更高的等离子体密度和电子温度)。在沉积DLC过程中,作为离子流参数的基体偏流超过5A。
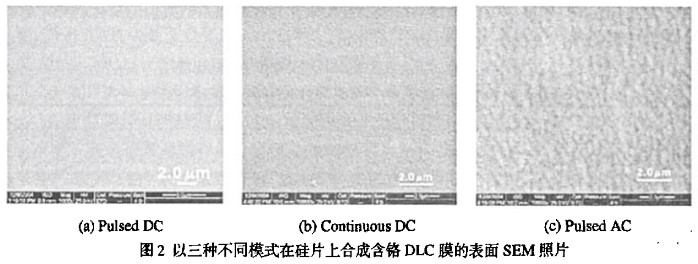
2.1表面形貌
图2显示以三种不同模式在硅片上DLC膜的表面SEM照片,从图中可以看出,在三种模式下合成DLC膜的表面形貌差异很大。在类似沉积条件下,脉冲模式下形成薄膜表面更加平滑,在脉冲DC模式下最为平滑。薄膜平均表面粗糙度Ra的测量值和观测结果一致,在连续DC模式下薄膜Ra为25nm,脉冲AC模式下的是10nm,而在脉冲DC模式下的是4nm。
2.2显微硬度
三种不同模式下合成含铬DLC膜的显微硬度测试结果显示,在脉冲AC模式下合成含铬DLC膜显微硬度的三次平均值为25.62GPa,在脉冲DC模式下的为26.66GPa,而在连续DC模式下的为13.13GPa。即,在脉冲模式下台成含铬DLC膜的显微硬度约是在连续DC脉冲下的两倍,而在两种不同脉冲脉冲下合成薄膜的显微硬度差异不大。
2.3结合力
划痕试验结果表明在脉冲模式下DLC膜和M2基体之间的结合力要比在连续DC模式下的要高。DLC膜的三次平均临界载荷Lc,脉冲DC漠式下的为55N,脉冲Ac模式下的为40N,而在连续DC模式下的为25N。以三种模式在M2基体上合成DLC膜划痕失效区域的光学显微镜照片示于图3。如图3c所示,连续DC模式下DLC膜以裂纹形式失效,并带有一些剥离;在脉冲模式下的示于图3a和图3b,在脉冲DC脉冲下的在划痕失效区域仍然保持较为完整的薄膜,只有少数轻微剥落痕迹。
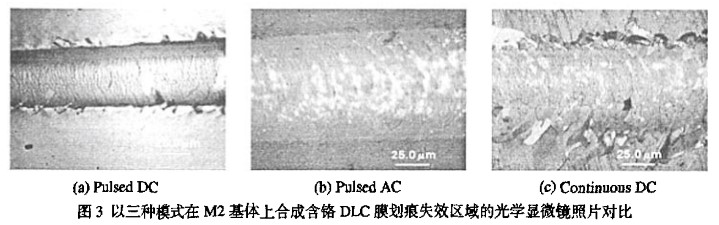
2.4摩擦性能
以三种模式合成DLC膜的球一盘试验结果示于图4。从图中可以看出,在同样200m滑动距离中,在脉冲模式下合成DLC膜的摩擦系数要比在和连续DC模式下合成薄膜的摩擦系数低,其中在脉冲AC模式下合成DLC膜的平均摩擦系数为O.11,脉冲DC模式下DLC膜的平均摩擦系数为0.09,而在连续DC模式下的为0.18。薄膜的磨损率亦有和摩擦系数类似的变化趋势,脉冲DC模式下DLC膜的磨损率最低。
2.5反向电压幅值和持续时间
反向电压幅值和持续时间可能是影响合成DLC膜摩擦学性能的重要因素(即空位电压)。在40kHz条件下,起弧现象得到了抑止,当反向电压持续时间增加至和占位时间相同时,灭弧效果好。通过以上图示中Dc模式和AC模式的对比结果中可以看出,反向电压的幅值也对DLC性能亦有明显影响:由于没有反向电压,在连续DC模式中DLC膜的性能较差;脉冲AC模式中薄膜的性能不如脉冲Dc模式中的薄膜性能,可能和反向电压过大有关;在脉冲IX:模式中得到薄膜的性能最好,可能在于其反向电压保持在磁控靶正常工作电压的10%。估计带有适宜反向电压持续时间和幅值的非对称双极脉冲磁控溅射可制备出高质量的DLC膜。
3.结论
在三种不同非平衡磁控溅射模式分别合成了性能各异的含铬DLC膜。和连续DC模式下的相比,通过采用脉冲AC和DC膜式,特别是脉冲DC模式,含铬DLC膜的综合性能得到显著提高。在脉冲DC模式下,合成DLC膜具有优越的综合摩擦学性能:平滑表面、26.66GPa的高硬度、55NLc的良好结合力和0.08的低摩擦系数。三种模式中的反向电压幅值和持续时间和DLC膜的性能差异相关。带有适宜反向电压持续时间和幅值的非对称双极脉冲磁控溅射可能成为提高DLC膜性能的一种有效方法。