高速切削刀具用物理气相沉积涂层研究进展
2023-02-10
涂层刀具是利用气相沉积方法在高强度的硬质合金或高速钢(HSS)基体表面涂覆几个微米的高硬度、高耐磨性的难熔金属或非金属化合物涂层而获得的,涂层刀具具有表面硬度高、耐磨性好、化学性能稳定、耐热耐氧化和摩擦系数小等特性。涂层材料作为化学屏障和热屏障,减少了刀具与工件间的扩散和化学反应,减少了月牙洼磨损,提高了涂层刀具使用寿命和切削效率。高性能涂层刀具已成为现代刀具的标志,目前发达国家涂层刀具在刀具中所占比例已超过80%,并不断上升。
刀具涂层的制备技术分为化学气相沉积(CVD)和物理气相沉积(PVD)两类,CVD技术存在反应气体腐蚀设备、环境污染等一系列问题,自20世纪90年代中期以来其发展和应用受到一定制约。物理气相沉积(PVD)技术对环境无不利影响,在控制涂层的组元成份和结构方面具有优势。刀具涂层材料和涂层技术在不断升级更新,目前的刀具涂层已发展为添加多种功能化元素(抗磨损、耐氧化、低摩擦),具有多种结构(纳米多层、纳米复合、梯度或多层结构等)的多元多层纳米复合涂层。本文对用于高速切削刀具的新型PVD涂层材料和沉积工艺进行了回顾和展望。
刀具表面的硬质涂层对材料有以下要求:(1)硬度高、耐磨性好;(2)化学性能稳定,不与工件材料发生化学反应;(3)高温抗氧化性和热稳定性高,在高温下还能保持高硬度和长期稳定性;(4)与基体结合强度高,摩擦系数低。因此适合做刀具涂层的材料主要是过渡金属的氮化物和碳化物(TiN、TiC、CrN等),此外还有一些共价键化合物(金刚石、BN等)和离子键化合物(Al2O3)。TiC和TiN是最早出现的刀具涂层材料。TiC涂层抗磨料磨损能力强,具有高的抗刀面磨损和抗月牙洼磨损能力;TiN涂层摩擦系数小,应用温度高于TiC,适于加工钢材或切削易于粘在前刀面上的材料。随着现代高速高效加工和难加工材料日益增多对刀具材料的苛刻要求,TiC和TiN涂层的硬度和抗高温能力已满足不了加工需要。刀具涂层材料不断升级更新,经历了简单二元涂层(TiN、TiC)→三元或四元固溶涂层(TiAlN、TiCN、TiAlCN等)→多层或超晶格结构涂层(TiN/TiC/TiN多层、多层、TiN/AlN超晶格等)→纳米复合结构涂层(TiSiN、等)的发展,涂层的硬度和最高使用温度不断提高。图1和图2总结了近年来出现的新型涂层和涂层性能的发展。
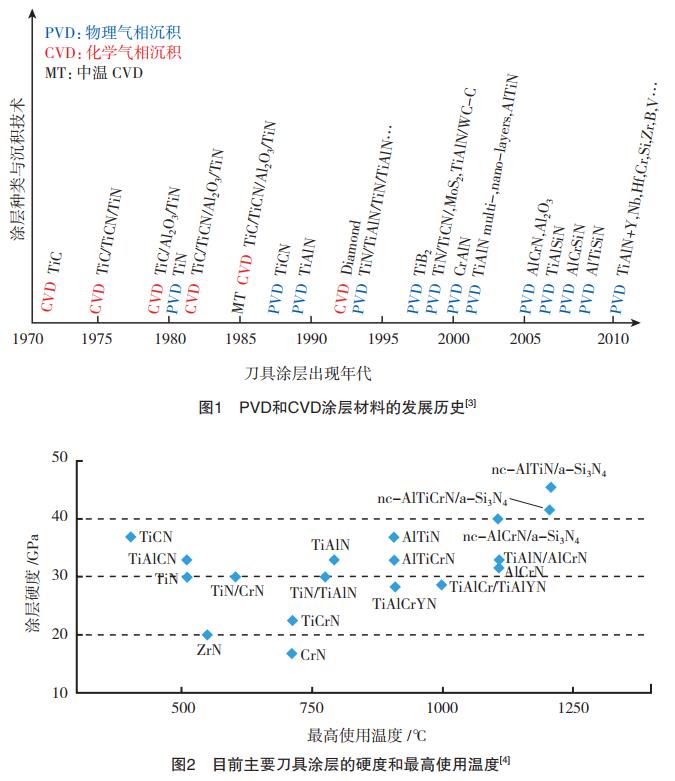
1、多元涂层
在TiN等二元涂层中加入第三或者第四元素制备出多元的刀具涂层材料后,大大提高了刀具的综合性能,如加入Cr和Y提高抗氧化性,加入Zr、V、B和Hf提高抗磨损性,加入Si提高硬度和抗化学扩散。最常用的多元刀具涂层是TiCN、TiAlN、涂层。TiCN涂层兼有TiC和TiN涂层的良好韧性和硬度,它在涂覆过程中可通过连续改变C和N的成分来控制TiCN的性质,并可形成不同成分的梯度结构,降低涂层的内应力,提高韧性,增加涂层厚度,阻止裂纹扩展,减少崩刃。近年来,以TiCN为基的四元成分新涂层材料(如TiZrCN、TiAlCN、TiSiCN等)也纷纷出现。
TiAlN涂层材料是目前应用最广泛的高速硬质合金刀具涂层之一,TiAlN有很高的高温硬度和优良的抗氧化能力,涂层组成由原来的Ti0.75Al0.25N发展到和Ti0.33Al0.67N。AlTiN涂层在900℃时才会出现硬度降低;在高速加工产生的高温下表面会产生一层非晶态Al2O3薄膜,对涂层起保护作用。
AlCrN系列涂层是近10年发展最为迅速的刀具涂层之一,与涂层相比,由于受到涂层结构稳定性的限制,AlTiN涂层中的铝含量实际已达到最大值(约66%)。在CrN基涂层中,铝含量可以进一步提高到70%。在温度达到1000℃时仍可保持其硬度;涂层具有较低的导热系数;在1100℃下还可以保护刀具基体不发生氧化。其韧性超过钛基涂层(如TiAlN、TiCN),更适合断续切削和难加工材料的加工。
在TiAlN和AlCrN涂层基础上加入Cr(Ti)、B、Y、Zr等元素可以实现刀具涂层性能的进一步改善。可以通过硼含量的变化,在加工过程中产生所谓“实时”现象,即通过硼扩散,形成BN、B2N3,从而得到有利于切削加工的润滑膜层。也可以在AlCrN涂层的基础上,推出TiAlN+AlCrN基的涂层,完美的基础涂层保证了卓越的结合力和加工强度,纳米结构的AlCrN涂层表现出良好的红硬性和抗高温氧化性能。
2、纳米超硬涂层
纳米结构涂层因具有高硬度和其他特性而成为刀具涂层发展方向,主要分为两类,一种是纳米多层涂层,如TiN/AlN,TiN/TiAlN等。日本某公司开发的AC105G、AC110G等牌号的ZX涂层是一种TiN与AlN交替的纳米多层涂层,层数可达层,每层厚度约为1nm。这种涂层与基体结合强度高,涂层硬度接近CBN,抗氧化性能好,抗剥离性强,而且可显著改善刀具表面质量,其寿命是TiN、TiAlN涂层的2~3倍。纳米多层涂层的硬度增强不但与单层材料的性能和制备工艺有关,还与涂层的调制周期有关,当在形状复杂的刀具或统一装炉中不同工件表面沉积时很难控制各层的厚度,而且在高温工作环境下各层间的元素互扩散也导致涂层性能发生变化,因此,不适合作为广泛推广的高速切削刀具涂层。另外一种是纳米复合涂层,纳米的硬质氮化物晶粒弥散地分布在晶态或者非晶态的第二相基体中,主要有氮化物/金属相纳米复合涂层(nc-MeN/nc-Me’,Me:Ti、Cr等,Me’:Cu、Ni等)和氮化物/非晶相纳米复合涂层(Me-Si-N,Me:过渡金属元素及其组合或与Al等元素的组合,如Ti、TiAl等),氮化物/金属相系统热稳定性差,在高温下易扩散导致硬度下降,不适合作刀具涂层。
Me-Si-N纳米复合涂层通过在传统的TiN和TiAlN等单相涂层中加入一定含量的Si元素,发生热力学上的调幅分解,生成由1~2个非晶原子层(Si3N4)包覆纳米晶过渡金属氮化物(TiN,TiAlN等)的骨架式纳米复合结构(图3),由于纳米晶体的强化效应及非晶层限制晶粒的滑移和转动对纳米晶晶界的强化作用,涂层表现出传统硬质涂层难以达到的高硬度,而且涂层高温下的组织稳定性、热硬性和抗氧化性等性能也大幅度提高,适应于高速切削条件下对涂层性能的苛刻要求;在涂层中加入各种第四和第五元素,可以进一步改善涂层的硬度、韧性、摩擦系数和高温抗氧化性等。纳米复合涂层代表了国际上新一代刀具涂层发展的方向。
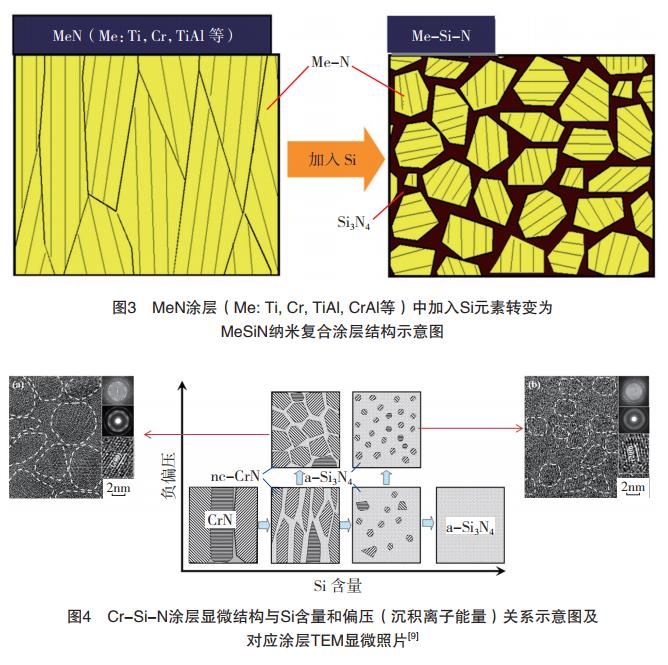
PVD技术制备Me-Si-N纳米复合涂层的难点在于对纳米相晶粒大小、形状和分布、非晶相厚度的控制,等通过沉积涂层的成分和离子能量的控制(图4),实现了纳米复合涂层的可控生长;余东海等采用空心阴极和磁控溅射复合离子镀技术制备了TiAlSiN、TiCrSiN多元纳米复合涂层刀具,高速銑削淬硬钢取得较好效果。
部分公司开发了纳米复合结构的刀具涂层。S.Carvalho等采用直流反应磁控溅射方法制备了纳米复合涂层刀具,并将该涂层与目前市场上适合高速切削的多层涂层(TiCN/Al2O3/TiN)的切削性能进行了比较,结果显示,TiAlSiN纳米复合涂层刀具在Vc=200m/min的条件高速车削合金钢,比TiN多层涂层刀具磨损小,且工件表面粗糙度小于4μm,比TiN多层涂层刀具加工的工件表面质量(12μm)有很大提高。P公司的新一代nc-Ti1-xAlxN/(a-Si3N4)纳米复合涂层刀具,是在强等离子体作用下,3nm的TiAlN晶体被镶嵌在非晶态的Si3N4体内,晶粒之间为1nm厚的Si3N4。这种结构使涂层硬度可达到50GPa,摩擦系数为0.45,且高温硬度更是非常突出,最高使用温度可达1100℃,温度达到时,其硬度值仍可保持在30GPa。日本公司开发的TiSiN涂层刀具(“TH”涂层)改善了加工高硬度材料时,TiN涂层刀具长期以来未能解决的涂层氧化和硬度欠佳问题。用“TH”涂层刀具高速加工拉伸模材料(HRC62)时与TiAlN涂层刀具相比加工成本降低54%。表1列出了几种纳米复合涂层与传统TiN和TiAlN涂层的性能对比。
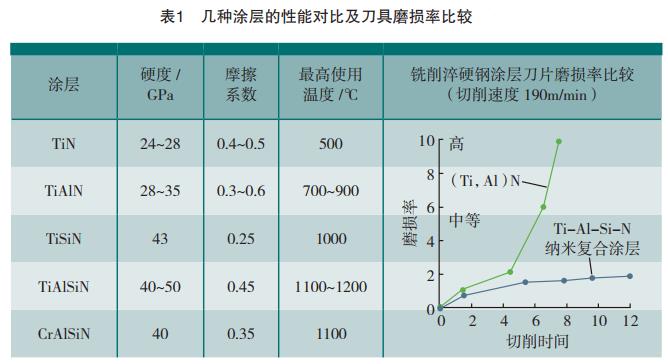
3、梯度和多层涂层
梯度涂层可以提供基体与涂层热膨胀系数和力学性质的过渡,降低内应力,改善涂层的结合强度和韧性,在高速切削的重载荷下使涂层不易崩裂和剥落,现代刀具涂层多采用多层或渐变式结构;通过梯度涂层的设计可以避免灾难性的刀具涂层疲劳失效,极大延长涂层寿命,多层涂层(这里不含纳米多层涂层)的设计主要是考虑刀具涂层更好的结合和多功能化,在CVD涂层中常采用3~7层涂层的组合方式,如,底层的TiC与基体的结合强度高,并有良好的耐磨性;中间的Al2O3作为一种有效的热屏障可允许有更高的切削速度;外层的TiCN保证抗前刀面和后刀面磨损能力;最外一薄层金黄色的TiN使得容易辨别刀片的磨损状态。PVD涂层中也经常采用多层结构,如的TripleCoatings三重涂层(nACo3、、nATCRo3)由Ti(Cr)N粘结底层(良好结合)、AlTi(Cr)N中间层(坚固核心和良好耐磨性、较低内应力)和AlCrSiN纳米结构顶层构成(极高硬度、出色隔热性和抗磨损能力)构成,通过成分和结构调整可以实现各种条件下的高速切削。
在刀具涂层表面产生磨擦系数低的表面层,可以实现降低切削力和降低切削温度,从而改善切削性能。一种是直接沉积固体润滑膜,如DLC、MoS2基的软涂层材料,但是由于该类涂层耐温一般都比较低,难以适应高速重载荷切削的需要,但在加工某些有色金属时具有良好的效果。如某公司新推出的软涂层,在TiN硬涂层基础上涂覆一层0.2~0.5μm厚的减摩涂层,摩擦系数仅为0.05~0.10,具有不粘附和自润滑的作用,避免加工高塑性、高韧性工作材料时出现粘刀及积屑瘤现象,非常适合于干式或微量润滑条件下钻削加工铝合金、钛合金等轻金属材料。另外一种是加拿大McMaster大学教授提出来的自适应涂层的思想,他提出通过涂层成分和结构设计使涂层在使役过程中自适应环境生成具有抗氧化性、低摩擦系数而且有利于耗散能量的复合氧化涂层。以此思想成功研制了性能远优于nc-AlTiN/a-Si3N4纳米复合涂层的TiAlCrSiYN和NbN自适应纳米涂层,高速切削时涂层表面很容易生成含有适当含量Cr-O、Al-O、Si-O的氧化膜,既具有抗氧化性,又具有自润滑性能,降低了刀具切削力和温度,改善其切削性能;Nb-O氧化膜电阻率接近金属,可以快速将积聚的变形能传递出去,不对氧化膜下面的涂层产生破坏。对PVD技术沉积的AlTiN涂层表面进行Ar+离子轰击处理,增加涂层表面的缺陷和活性,在高温切削时生成类α-Al2O3薄膜,涂层高温下的摩擦系数有明显降低,高速切削性能有较大改善。
4、含氧涂层
涂层沉积过程中,真空室内总存在一定的残留气体,Nakano等在用超高真空反应磁控溅射沉积TiN涂层时发现,只有在真空达到10-8Pa量级的时候,涂层中才不含氧,当氧分压为10-4Pa量级的时候,用X射线光电子能谱(XPS)还可以检测到涂层中含10%~20%(摩尔分数)的氧,尽管测得氧含量的绝对数值会随测量方法有差异,但可以确定涂层中含有相当含量的氧杂质。对于一般工业型硬质涂层沉积设备,真空度基本在10-3Pa量级,涂层会不可避免地含有一定量的氧,所以氧对刀具涂层结构和性能的影响是无法回避的问题,尽管在大部分的研究中并没有对这个问题加以重视。
有关氧对刀具涂层结构和性能的影响,基本上有两类观点,一种认为涂层中氧杂质是有害元素,会引起涂层硬度下降,Veprek等在研究纳米复合涂层时发现其同一成分和结构的TiSiN涂层硬度变化可以很大。通过研究涂层中杂质含量,认为是包括沉积参数和杂质含量等导致超硬涂层硬度值的分散,其中杂质含量影响最大,只有当杂质元素含量小于0.01%时才可能复制出他的试验结果。马大衍等报道氧含量0.1%和0.2%时可以分别达到60GPa和50GPa的硬度,氧含量时涂层最高仅30GPa左右,没有明显的硬度增强效应。另一类学者认为氮化物涂层中含有一定量的氧并不一定会导致性能的下降,如果对涂层中氧元素加以利用,可以获得良好的切削刀具涂层。通过氧的加入可以改善CrN涂层的抗氧化性能,可以在不降低或略有降低硬度的前提下改善其摩擦性能,从而使TiAlON涂层的切削性能比有所提高。Ding等在非平衡磁控溅射TiSiN涂层中加入氧元素,在O/N为0.72时摩擦系数可以降低至20%,而硬度降低不大。Lee等提出一定量氧的加入可以调整涂层的内应力水平,降低摩擦系数,而硬度还可以略有升高。据悉,公司推出的TiAlXN涂层即为涂层,切削性能优于涂层。Barthelmä等研究电弧离子镀和ZrON涂层刀具,在等温淬火球铁和不锈钢等难加工材料的高速加工上显示优势。
氧化物的高温稳定性明显优于氮化物,当涂层以氧化物为主时,涂层在高温下的表现更佳,其中代表是氧化铝涂层。Al2O3具有高耐磨损性和红硬性,在1000℃仍能保持良好化学稳定性。在切削刀具表面制备Al2O3涂层,能够在高速干切削条件下对刀具起到保护作用,从而提高切削加工效率。部分公司已制备出涂层可用于高速切削刀具,但PVD氧化物涂层的经济性仍存在问题;P公司采用更为经济的氧化物涂层,发展了AlCrON和涂层,涂层仍以氧化物为主,但由于加入Cr和N,更容易沉积制备。由于氧化物的特点是化学稳定性好、高温性能好、抗扩散磨损性能好,但韧性较差,作为刀具涂层一般是加在、TiAlSiN等硬质支撑层表面使用。
目前,用于硬质涂层沉积的PVD涂层技术主要有磁控溅射和电弧离子镀两类。传统的磁控溅射技术因其低温沉积、表面光滑、无颗粒缺陷等诸多优点,是目前最重要的工业化大面积真空镀膜技术之一。但溅射金属大多以原子状态存在,金属离化率低(约1%),导致膜基结合力较差,涂层易剥落失效。相比于磁控溅射,电弧离子镀具有较高金属离化率(约90%)和强膜基结合力的优点;然而,在沉积过程中产生的大量宏观颗粒,导致涂层表面粗糙、内应力高。PVD涂层技术在20世纪末和进入21世纪后经历了革命性发展,新型磁控溅射技术的发展,如将高能脉冲溅射沉积技术、双极脉冲磁控溅射、气体反馈控制系统和闭合磁场设计等新技术应用于硬质涂层产业,可制备出硬度高、均匀致密、结合强度高、内应力低、韧性好的硬质涂层;而且方便控制硬质涂层的组元成分和结构,沉积出各种符合要求的涂层。与此同时,电弧离子镀技术也有很多大的改进,通过增大阴极面积,采用旋转阴极和采用激励磁场分散电弧的办法,大大降低了涂层中的大颗粒含量。
高功率脉冲磁控溅射技术(HIPIMS)是近年来发展起来的一种高离化率PVD技术,该技术是利用较高的脉冲峰值功率(传统磁控溅射的1000倍或更高)来实现产生高金属离化率(>50%)。高功率脉冲磁控溅射技术综合了磁控溅射表面光滑、无颗粒缺陷和电弧离子镀离化率高、膜基结合力强、涂层致密的优点,且离子束流不含大颗粒,在控制涂层微结构的同时获得优异的膜基结合力,在降低涂层内应力,以及提高涂层致密性、均匀性,尤其是对复杂几何形状工件沉积材料到不同区域的导向等都具有显著的技术优势,被认为是PVD发展史上近30年来的最重要的一项技术突破。Lattemann等采用HIPIMS离子轰击,在CrN/NbN纳米多层涂层与高速钢基体之间生成冶金结合的界面,界面结合力远优于Ar离子轰击和电弧轰击;等发现不同的HIPIMS离子轰击种类(Ti、W、Cr)对硬质合金刀具上涂层的界面结合强度、界面应力、涂层疲劳强度和刀具切削性能有至关重要的影响。Bobzin等采用技术(高束流离子轰击加速纳米复合涂层的Spinodal调幅分解)制备TiSiC、TiAlSiN等纳米复合涂层,形成两相完全分离的纳米晶/非晶复合结构,有利于硬度和韧性同步改善,使刀具寿命提高近1倍。技术在合成r-TiO2、a-Al2O3、(MAX)等不易在室温下生成的高温相方面也具有优势。
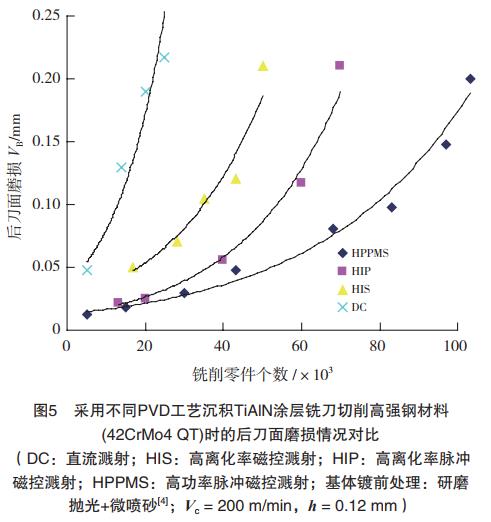
结束语
由于现代高速高效加工和难加工材料使用日益增多对刀具材料的苛刻要求,国际上刀具涂层材料和涂层技术在不断升级更新,目前的刀具涂层已发展为添加多种功能化元素(抗磨损、耐氧化、低摩擦)、具有多种结构(纳米多层、纳米复合、梯度或多层结构等)的多元多层纳米复合涂层;传统的电弧离子镀和磁控溅射技术经过多种改进,可以制备出硬度高、均匀致密、结合强度高、内应力低、韧性好的硬质涂层,用于刀具涂层生产。