等离子增强磁控溅射技术
2019-07-11
等离子增强磁控溅射(Plasma Enhanced Magnetron Sputtering)沉积技术,简写为PEMS,是物理气相沉积(PVD)技术的一种,是在传统磁控溅射技术的基础上做了改进,使膜层更加致密,硬度更高,韧性和结合力更好。它与传统磁控溅射(Conventional Magnetron Sputtering,简写为CMS)的区别在于其运用独立的电子发射源达到等离子体增强的效果,制备出的涂层致密度、硬度和韧性等均有显著提高。运用PEMS技术可以制备传统磁控溅射技术的所有涂层,如TiN,CrN,TiAlN,TiCN等,以下介绍PEMS的原理和特点。
(一)PEMS技术的原理
PEMS技术结合传统磁控溅射技术的优点,在其基础上做了改良,图1为PEMS技术的原理图和实际镀膜工作时的图片。如图1(a)所示,真空室左右两边分别有一个圆柱形金属靶,在真空室的中央,有一个旋转的工作台便于悬挂工件。PEMS技术应用了一个电子发射源来产生更多的电子,一般选用加热的钨丝或者空心阴极管作为电子发射源。从实际工作图1(b)的下方可以隐约看见耀眼的光线,即钨丝在加热状态发出的光线。当真空室内气压到达几个毫托,在钨丝和真空壁之间施加直流放电电压(DC Discharge Power Supply),即:真空壁接地,钨丝上为恒定负偏压。同时,在钨丝上加载交流电,钨丝被加热后向真空室内释放电子,在放电电压的作用下,电子被加速向真空壁飞去,由于真空室内存在大量的气体分子(Ar,TMS,N2等),电子与中性气体分子(原子)发生碰撞,导致气体电离,并最终使真空室内产生等离子体。PEMS与传统的MS的主要优势就是由引入的灯丝导致的,它使整个真空室产生了等离子体(Global Plasma),而传统的MS所产生的等离子体只是局限在磁控溅射的靶之前,这个GlobalPlasma极大地增强了等离子的密度,等离子体中带正电的Ar离子受到靶材的吸引,轰击靶材产生溅射。所以,等离子体的增加可以提高溅射速率,同时基片也可以吸引充满于整个真空室的Ar,其不断的轰击使膜层的致密度和结合力增强。
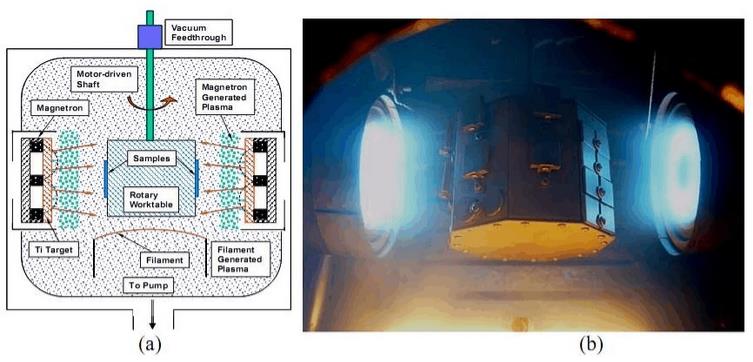
(a)PEMS技术的工作原理图 (b)实际镀膜工作图
从图1(a)可以看出,PEMS原理图的下半部分有一个灯丝,通常使用钨丝。在交流电加热下,钨丝不断释放电子,它独立于磁控管。因此,在工件清洗和镀膜过程中,它可以实现传统磁控溅射没有的功能。在PEMS工件清洗过程中,磁控管保持关闭状态,此时真空室内Ar的气压保持几个毫托,在钨丝上加载交流电,并在工件上缓慢增大负偏压,灯丝上释放出的电子向真空壁加速,与Ar碰撞后使整个真空室内充满Ar等离子体,这时在工件上加载的负偏压将带正电的离子吸到工件表面,在离子的轰击下降其表面清洗干净。需要指出,工件表面的负偏压需要缓慢增加,调节过快表面会出现电弧,对工件的新鲜表面很不利。清洗完毕,在不关闭钨丝电源的情况下开启磁控管,这样在清洗和镀膜之间避免了气压过渡过程,工件表面不容易被氧化。
在镀膜过程中,金属蒸汽沉积到工件表面形成金属膜,此时,在工件上加有的负偏压将氩离子拉到涂层上进行轰击,提高了膜的致密性和结合强度。需要强调的是,镀膜过程中钨丝产生的等离子体是独立于磁控管产生的等离子体的,经法拉第杯(FaradayCup)试验测定,发现有钨丝的离子电流密度是单独磁控管产生离子电流密度的25倍,足够的电流密度为镀膜过程中提供了充足的能量,膜的致密度显著提高。
(二)CMS和PEMS实验结果比较
为了深一步研究PEMS技术,美国西南研究院魏荣华等人使用CMS和PEMS两种方法,运用几乎相近的实验参数在Si片表面镀上Cr涂层。
图2为涂层表面和横截面SEM形貌,其中左侧运用的是CMS技术,右侧是PEMS技术。从表面形貌可以看出,采用传统磁控溅射CMS沉积出来的Cr涂层表面粗糙,晶粒比较粗大;从横截面上看,CMS沉积的涂层呈现出典型的柱状结构,致密度低。相近参数下,PEMS技术沉积的Cr涂层表面光滑,无明显的柱状结构,而且非常致密。这是由于热钨丝释放的电子增加了等离子体密度,剧烈的离子轰击靶材使得涂层的致密度增加。
(三)离子增强磁控溅射技术的应用
1、等离子增强磁控溅射技术在刀具上的应用
在机械加工过程中,传统的单相(Single Phase)的一些硬膜,包括TiN,TiCN,TiAlN以及其他硬的碳、氮化合物涂层,很早就开始用于提高刀具的性能,各种物理气相沉积PVD技术已经运用于制造这类涂层。随着工业的发展,对刀具的要求越来越苛刻,切削速度越来越高,同时对环境的要求也越来越严格,无切削液的的干式加工已经提到日程。理想的刀具需结合高硬度,韧性和高温稳定性于一体,在这三项指标中,硬度和韧性往往是一对矛盾的参量,高硬度通常伴随着是脆性的增加,目前还没有很好的刀具能同时兼顾韧性和硬度的指标。人们在高韧性的基体上镀上耐磨涂层,厚度为3~10μm,以此来实现硬度和韧性的结合,随着研究的深入,人们对涂层的组织结构和厚度的优化来进一步提升性能。
Luca Settineri等人对两种超硬纳米复合涂层的力学性能和摩擦学特性进行了研究,与传统TiN涂层比较,发现纳米复合涂层的硬度,韧性和寿命都显著提高,其摩擦系数在0.8左右,但磨痕宽度和深度都比TiN大。美国西南研究院的魏荣华博士发明了等离子增强磁控溅射技术,首次在溅射过程引入三甲基硅烷(TMS)气体沉积TiSiCN超硬纳米复合涂层,研究发现韧性的增加对涂层的综合性能提升显著,镀有TiSiCN超硬纳米复合涂层刀具的寿命是普通商业镀膜刀具寿命的4倍以上。
2、等离子增强磁控溅射技术在耐冲蚀领域的应用
飞机发动机和汽轮机叶片,以及鼓风机叶轮等工件在恶劣环境下(固体颗粒,水滴等)长时间工作会产生严重磨损,导致稳定性和可靠性降低。人们在其表面镀过各种涂层来试图延长寿命,包括最硬的材料金刚石到很软的材料环氧树脂。商业上人们使用得较多的有单相的TiN,CrN,ZrN,TiAlN涂层;双层的Ti/TiN,Cr/CrN,W/WC,TiN/TaN;以及超晶格的CrN/NbN等,工业上制备这些涂层的方法一般使用磁控溅射(MS)和阴极电弧蒸发技术(CAE)。
考虑到金属有机物气体对人体的危害性,使用CVD的方法来制备含有金属的涂层发展缓慢。自等离子技术应用到CVD之后,较硬的DLC(DiamondLikeCarboncoating)薄膜由此诞生,人们称这种技术为PECVD或PACVD(PlasmaAssistedChemicalVaporDeposition)。由于镀膜过程中使用的气体都是甲烷,乙炔,TMS等有机气体,DLC膜的主要成分是碳和固态的氢,它拥有硬度高、摩擦系数小、室温和高温稳定性好、耐腐蚀、不导电等优点。另外,在镀膜过程中其操作简单,低温下工作对基体材料热破坏效应小,而且具有工件无需旋转,镀膜效率高等优势。对于PECVD的一个最为重要的特点是,它可以将非常复杂的3-D工件的任何表面都镀上膜。因此,商业上使用DLC膜作为鼓风机叶轮等工件的保护涂层效益巨大。
3、等离子增强磁控溅射技术在耐腐蚀领域的应用
油气管道、海水环境工作下的发动机叶片以及在含有硫化氢,氨气,二氧化碳等酸碱气体下的工件长时间工作会产生电化学腐蚀,最终会造成严重的经济损失,甚至会威胁到操作人员的安全。因此,如何提高工件的电化学稳定性变得十分重要。
早期人们发现TiN涂层不仅具有好的力学和光学性能,其耐腐蚀性能也较好,随着研究的深入,科学家们在TiN的基础上制备了TiAlN,TiCrN,CrAlN以及TiZrN等三元乃至四元的涂层。Penttinenetal.使用物理气相沉积的方法在不锈钢(AISI316)基体上分别镀上TiN和TiAlN涂层,采用阳极极化和恒电位测量的方法来研究这两种涂层的耐腐蚀性能。研究发现,当这两种涂层与基体的界面形成一层含Cr或者Cr的氧化物的过渡层时,涂层具有最好的腐蚀阻力。Jenhetal.在304不锈钢基体上沉积(TiCr)Nx薄膜,并在中性PH值或者弱酸性溶液中(Na2SO4和NaCl)做了电化学测试,发现与TiN涂层相比,含有Cr的涂层耐腐蚀性能更好。
4、等离子增强磁控溅射技术在模具上的应用
汽车工业是世界工业的重要支柱产业之一。铝合金是汽车上使用得较多的材料,其质地轻,强度较高,而且耐氧化。在实际制备这些汽车零部件的时候,会发现液态的铝和模具之间粘合严重,造成脱模困难。
铸铝模具在生产的时候会受到不同程度,不同机理的破坏。经过长期的研究人们发现,除了热处理和电镀化学镀,在铸铝模具表面镀上硬涂层也可以很好的保护模具表面。铝制工件和模具之间会产生化学粘附,而且铝会侵入到模具,最终导致难于脱模。而且,液态铝合金在注入、冷却、脱模过程中,温度频繁的变化会产生严重的热疲劳,并最终导致热裂纹。模具表面的损坏最终会导致整块模具失效,带来了巨大的经济损失。通常,粘附在模具表面的铝会以机加工的方式去除,一段时间后,模具也就因为各方面的原因而不能继续使用,如出现裂纹,精度差,表面粗糙度高等。适当的表面处理可以显著提高其性能和寿命,硬纳米复合涂层可以防止液态铝的侵蚀,提高热开裂的抗力,并能延缓裂纹的形成和拓展同时,最关键可以使液态铝和模具之间的粘结力降低。
(一)PEMS技术的原理
PEMS技术结合传统磁控溅射技术的优点,在其基础上做了改良,图1为PEMS技术的原理图和实际镀膜工作时的图片。如图1(a)所示,真空室左右两边分别有一个圆柱形金属靶,在真空室的中央,有一个旋转的工作台便于悬挂工件。PEMS技术应用了一个电子发射源来产生更多的电子,一般选用加热的钨丝或者空心阴极管作为电子发射源。从实际工作图1(b)的下方可以隐约看见耀眼的光线,即钨丝在加热状态发出的光线。当真空室内气压到达几个毫托,在钨丝和真空壁之间施加直流放电电压(DC Discharge Power Supply),即:真空壁接地,钨丝上为恒定负偏压。同时,在钨丝上加载交流电,钨丝被加热后向真空室内释放电子,在放电电压的作用下,电子被加速向真空壁飞去,由于真空室内存在大量的气体分子(Ar,TMS,N2等),电子与中性气体分子(原子)发生碰撞,导致气体电离,并最终使真空室内产生等离子体。PEMS与传统的MS的主要优势就是由引入的灯丝导致的,它使整个真空室产生了等离子体(Global Plasma),而传统的MS所产生的等离子体只是局限在磁控溅射的靶之前,这个GlobalPlasma极大地增强了等离子的密度,等离子体中带正电的Ar离子受到靶材的吸引,轰击靶材产生溅射。所以,等离子体的增加可以提高溅射速率,同时基片也可以吸引充满于整个真空室的Ar,其不断的轰击使膜层的致密度和结合力增强。
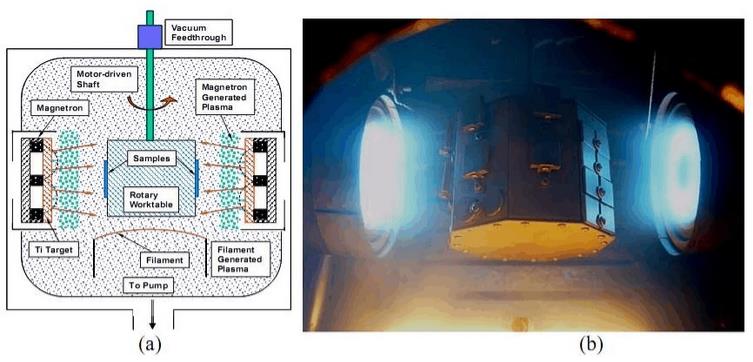
(a)PEMS技术的工作原理图 (b)实际镀膜工作图
从图1(a)可以看出,PEMS原理图的下半部分有一个灯丝,通常使用钨丝。在交流电加热下,钨丝不断释放电子,它独立于磁控管。因此,在工件清洗和镀膜过程中,它可以实现传统磁控溅射没有的功能。在PEMS工件清洗过程中,磁控管保持关闭状态,此时真空室内Ar的气压保持几个毫托,在钨丝上加载交流电,并在工件上缓慢增大负偏压,灯丝上释放出的电子向真空壁加速,与Ar碰撞后使整个真空室内充满Ar等离子体,这时在工件上加载的负偏压将带正电的离子吸到工件表面,在离子的轰击下降其表面清洗干净。需要指出,工件表面的负偏压需要缓慢增加,调节过快表面会出现电弧,对工件的新鲜表面很不利。清洗完毕,在不关闭钨丝电源的情况下开启磁控管,这样在清洗和镀膜之间避免了气压过渡过程,工件表面不容易被氧化。
在镀膜过程中,金属蒸汽沉积到工件表面形成金属膜,此时,在工件上加有的负偏压将氩离子拉到涂层上进行轰击,提高了膜的致密性和结合强度。需要强调的是,镀膜过程中钨丝产生的等离子体是独立于磁控管产生的等离子体的,经法拉第杯(FaradayCup)试验测定,发现有钨丝的离子电流密度是单独磁控管产生离子电流密度的25倍,足够的电流密度为镀膜过程中提供了充足的能量,膜的致密度显著提高。
(二)CMS和PEMS实验结果比较
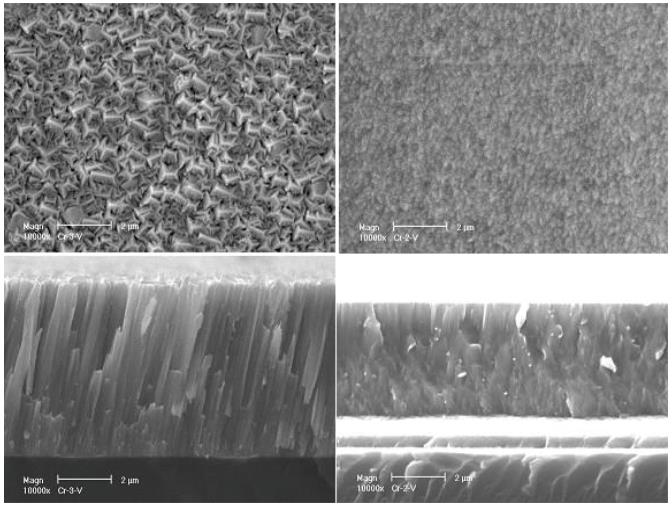
图2CMS技术(左)和PEMS技术(右)在硅片上沉积Cr涂层的表面形貌(上侧)和横截面(下侧)形貌图
为了深一步研究PEMS技术,美国西南研究院魏荣华等人使用CMS和PEMS两种方法,运用几乎相近的实验参数在Si片表面镀上Cr涂层。
图2为涂层表面和横截面SEM形貌,其中左侧运用的是CMS技术,右侧是PEMS技术。从表面形貌可以看出,采用传统磁控溅射CMS沉积出来的Cr涂层表面粗糙,晶粒比较粗大;从横截面上看,CMS沉积的涂层呈现出典型的柱状结构,致密度低。相近参数下,PEMS技术沉积的Cr涂层表面光滑,无明显的柱状结构,而且非常致密。这是由于热钨丝释放的电子增加了等离子体密度,剧烈的离子轰击靶材使得涂层的致密度增加。
(三)离子增强磁控溅射技术的应用
1、等离子增强磁控溅射技术在刀具上的应用
在机械加工过程中,传统的单相(Single Phase)的一些硬膜,包括TiN,TiCN,TiAlN以及其他硬的碳、氮化合物涂层,很早就开始用于提高刀具的性能,各种物理气相沉积PVD技术已经运用于制造这类涂层。随着工业的发展,对刀具的要求越来越苛刻,切削速度越来越高,同时对环境的要求也越来越严格,无切削液的的干式加工已经提到日程。理想的刀具需结合高硬度,韧性和高温稳定性于一体,在这三项指标中,硬度和韧性往往是一对矛盾的参量,高硬度通常伴随着是脆性的增加,目前还没有很好的刀具能同时兼顾韧性和硬度的指标。人们在高韧性的基体上镀上耐磨涂层,厚度为3~10μm,以此来实现硬度和韧性的结合,随着研究的深入,人们对涂层的组织结构和厚度的优化来进一步提升性能。
Luca Settineri等人对两种超硬纳米复合涂层的力学性能和摩擦学特性进行了研究,与传统TiN涂层比较,发现纳米复合涂层的硬度,韧性和寿命都显著提高,其摩擦系数在0.8左右,但磨痕宽度和深度都比TiN大。美国西南研究院的魏荣华博士发明了等离子增强磁控溅射技术,首次在溅射过程引入三甲基硅烷(TMS)气体沉积TiSiCN超硬纳米复合涂层,研究发现韧性的增加对涂层的综合性能提升显著,镀有TiSiCN超硬纳米复合涂层刀具的寿命是普通商业镀膜刀具寿命的4倍以上。
2、等离子增强磁控溅射技术在耐冲蚀领域的应用
飞机发动机和汽轮机叶片,以及鼓风机叶轮等工件在恶劣环境下(固体颗粒,水滴等)长时间工作会产生严重磨损,导致稳定性和可靠性降低。人们在其表面镀过各种涂层来试图延长寿命,包括最硬的材料金刚石到很软的材料环氧树脂。商业上人们使用得较多的有单相的TiN,CrN,ZrN,TiAlN涂层;双层的Ti/TiN,Cr/CrN,W/WC,TiN/TaN;以及超晶格的CrN/NbN等,工业上制备这些涂层的方法一般使用磁控溅射(MS)和阴极电弧蒸发技术(CAE)。
考虑到金属有机物气体对人体的危害性,使用CVD的方法来制备含有金属的涂层发展缓慢。自等离子技术应用到CVD之后,较硬的DLC(DiamondLikeCarboncoating)薄膜由此诞生,人们称这种技术为PECVD或PACVD(PlasmaAssistedChemicalVaporDeposition)。由于镀膜过程中使用的气体都是甲烷,乙炔,TMS等有机气体,DLC膜的主要成分是碳和固态的氢,它拥有硬度高、摩擦系数小、室温和高温稳定性好、耐腐蚀、不导电等优点。另外,在镀膜过程中其操作简单,低温下工作对基体材料热破坏效应小,而且具有工件无需旋转,镀膜效率高等优势。对于PECVD的一个最为重要的特点是,它可以将非常复杂的3-D工件的任何表面都镀上膜。因此,商业上使用DLC膜作为鼓风机叶轮等工件的保护涂层效益巨大。
3、等离子增强磁控溅射技术在耐腐蚀领域的应用
油气管道、海水环境工作下的发动机叶片以及在含有硫化氢,氨气,二氧化碳等酸碱气体下的工件长时间工作会产生电化学腐蚀,最终会造成严重的经济损失,甚至会威胁到操作人员的安全。因此,如何提高工件的电化学稳定性变得十分重要。
早期人们发现TiN涂层不仅具有好的力学和光学性能,其耐腐蚀性能也较好,随着研究的深入,科学家们在TiN的基础上制备了TiAlN,TiCrN,CrAlN以及TiZrN等三元乃至四元的涂层。Penttinenetal.使用物理气相沉积的方法在不锈钢(AISI316)基体上分别镀上TiN和TiAlN涂层,采用阳极极化和恒电位测量的方法来研究这两种涂层的耐腐蚀性能。研究发现,当这两种涂层与基体的界面形成一层含Cr或者Cr的氧化物的过渡层时,涂层具有最好的腐蚀阻力。Jenhetal.在304不锈钢基体上沉积(TiCr)Nx薄膜,并在中性PH值或者弱酸性溶液中(Na2SO4和NaCl)做了电化学测试,发现与TiN涂层相比,含有Cr的涂层耐腐蚀性能更好。
4、等离子增强磁控溅射技术在模具上的应用
汽车工业是世界工业的重要支柱产业之一。铝合金是汽车上使用得较多的材料,其质地轻,强度较高,而且耐氧化。在实际制备这些汽车零部件的时候,会发现液态的铝和模具之间粘合严重,造成脱模困难。
铸铝模具在生产的时候会受到不同程度,不同机理的破坏。经过长期的研究人们发现,除了热处理和电镀化学镀,在铸铝模具表面镀上硬涂层也可以很好的保护模具表面。铝制工件和模具之间会产生化学粘附,而且铝会侵入到模具,最终导致难于脱模。而且,液态铝合金在注入、冷却、脱模过程中,温度频繁的变化会产生严重的热疲劳,并最终导致热裂纹。模具表面的损坏最终会导致整块模具失效,带来了巨大的经济损失。通常,粘附在模具表面的铝会以机加工的方式去除,一段时间后,模具也就因为各方面的原因而不能继续使用,如出现裂纹,精度差,表面粗糙度高等。适当的表面处理可以显著提高其性能和寿命,硬纳米复合涂层可以防止液态铝的侵蚀,提高热开裂的抗力,并能延缓裂纹的形成和拓展同时,最关键可以使液态铝和模具之间的粘结力降低。