钨含量和摩擦条件对掺钨DLC涂层摩擦性能的影响
2024-03-20
真空离子镀膜类金刚石(DLC)涂层硬度高、表面光滑、摩擦系数低、耐磨性好,且在低温容易实现大面积沉积,在空天设备、精密机械、微型机电系统、工模具等领域具有广阔的应用前景。但DLC涂层存在内应力高、脆性大、膜/基结合力差等不足,这明显限制了DLC涂层的大规模应用;通过采用新型的制备方法和优化涂层结构等措施解决DLC涂层存在的主要技术难题,这对DLC涂层的应用具有重要意义。
降低DLC涂层内应力和改善膜/基结合力的方法包括基体表面改性、过渡层制备、DLC涂层的合金化、复合化和多层化[4,8,11]等。掺钨DLC涂层具有内应力低、膜/基结合力高、耐磨性好等优点,是具有广泛应用前景的DLC涂层。
尽管人们已经利用阴极电弧沉积、磁控溅射、等离子体增强化学气相沉积、离子注入、离子束沉积和脉冲激光烧蚀等方法制备出DLC涂层,开发新型的制备方法仍然是DLC涂层研究的一个重要领域。
DLC涂层的摩擦磨损性能与载荷、速度、对摩副材料、润滑条件、温度、湿度等因素密切相关,但目前对不同摩擦条件下掺钨DLC涂层的摩擦磨损性能的研究还不够充分,探讨摩擦条件对掺钨DLC涂层摩擦磨损性能的影响规律对DLC涂层在不同摩擦条件下的推广应用具有重要意义。
本研究利用磁控溅射+离子束沉积制备不同钨含量的掺钨DLC涂层,利用多种方法研究钨含量和摩擦条件对DLC涂层结构和性能的影响。
1、实验
试样基体材料为单晶硅Si(100)和316L不锈钢抛光片。利用阳极层长条离子源+磁控溅射方法制备掺钨DLC涂层,试验用气体为高纯氩气(99.99%)和高纯乙炔,溅射靶材为高纯钨。离子源工作参数根据优化的纯DLC膜离子束沉积工艺确定,利用磁控溅射实现DLC涂层的钨掺杂,通过改变靶电流来调整DLC涂层的钨含量。为了提高膜/基结合力,在DLC涂层沉积前首先利用阴极电弧+离子束辅助磁控溅射技术制备梯度过渡层。
利用SIRON-200型扫描电子显微镜观察DLC涂层的表面形貌。利用PHI700型俄歇扫描纳探针分析DLC涂层的成分。利用PHIQuanteraSXM型X射线扫描微探针分析DLC涂层的化学结合状态。利用MTSXP型纳米硬度仪测定DLC涂层的硬度和弹性模量。利用型多功能材料表面性能测试仪评价DLC涂层的膜/基结合力。利用MTS-3000型摩擦磨损实验机测试DLC涂层的摩擦系数,摩擦条件为:对磨件为直径的Si3N4球,载荷为0.49~4.9N,转速为100~600r/min,磨损半径为3mm,干摩擦。利用MicroXAM-3D型三维白光干涉表面形貌仪测定磨损体积并计算磨损率。
2、结果与分析
图1为靶电流对DLC涂层钨含量的影响曲线。从图可以看出,靶电流较低时,随着靶电流的增加,DLC涂层的钨含量缓慢增加;但当靶电流超过2.8A以后,DLC涂层的钨含量随着靶电流的增加而明显增大。其原因在于靶电流较低时钨靶表面被富碳的化合物沉积层覆盖,溅射出来的钨粒子较少;但当靶电流增大到一定程度后,钨靶表面的化合物沉积层被完全溅射掉,继续增加靶电流将使溅射出来的钨粒子明显增多,因而DLC涂层的钨含量随着靶电流的增加而显著增大。
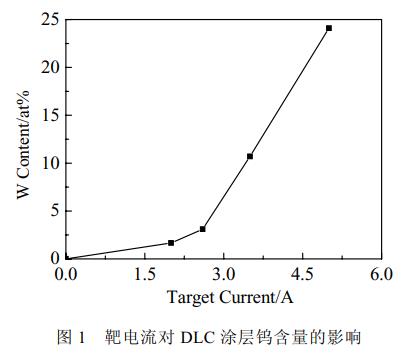
图2为不同钨含量的DLC涂层表面形貌。从图可以看出,掺钨DLC涂层光滑致密,但存在一些大小不一的颗粒和凹坑等缺陷,其尺寸在几百纳米到几个微米之间变化。它们主要是由过渡层制备过程中阴极电弧的喷射产生的,这导致DLC涂层的表面粗糙度明显增大,对进一步降低DLC涂层的摩擦系数不利。从图2还可以看出,不同钨含量的掺钨DLC涂层表面形貌差别不大,这是因为不同钨含量的DLC涂层的过渡层制备工艺相同。
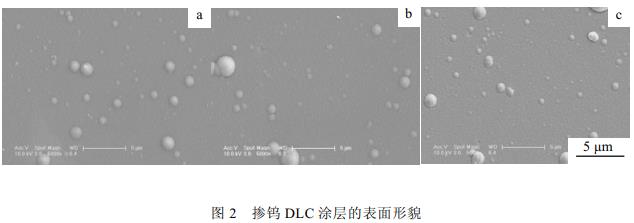
利用XPS的C1s谱可以计算出DLC涂层中不同结合状态的碳比例。图3为掺钨DLC涂层中不同结合状态的碳原子分数与钨含量的关系曲线。从图3可以看出,随着钨含量的增加,DLC涂层中以sp3键结合的碳原子分数逐渐降低,以sp2键结合的碳原子分数逐渐增加;这是由于引入钨原子减少了与碳配位的其他碳原子数所致。但当钨含量到达10%后,sp3键结合的碳原子分数不再降低,DLC涂层中发现了一定量的WC结合的碳原子,DLC涂层中生成纳米尺寸的WC有利于改善DLC涂层的韧性。
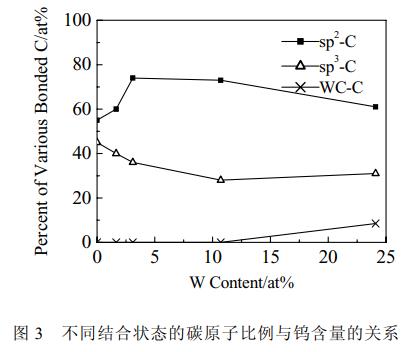
图4为钨含量对掺钨DLC涂层划痕法临界载荷的影响。从图可以看出,本研究制备的掺钨DLC涂层均具有良好的膜/基结合力(最低值为70N),且适当掺入钨元素可明显改善DLC涂层的膜/基结合力,最佳钨含量为3.1%(临界载荷超过100N)。这是由于适量掺杂钨显著降低了DLC涂层内应力所致,优异的膜/基结合力为掺钨DLC涂层在苛刻摩擦条件下的应用奠定了基础。
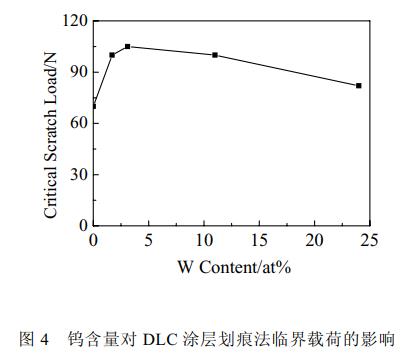
图5为掺钨DLC涂层的摩擦系数和磨损率与钨含量的关系。摩擦条件为:干摩擦,载荷1.96N,转速。从图5a可以看出,随着钨含量的增加,摩擦系数先明显增大,但钨含量超过3.1%后,钨含量的变化对DLC涂层的摩擦系数影响较小。其原因在于:钨含量较低时,DLC涂层中的钨原子与对摩副材料产生的粘着对摩擦系数的贡献随着钨含量的增加而强化,这导致摩擦系数随着钨含量的增加而增大;但钨含量超过3.1%后,粘着面积在实际接触面积中所占比例接近饱和,因而摩擦力变化不大。从图5b可以看出,随着钨含量的增加,DLC涂层的磨损率在钨含量为3.1%时出现了最小值。这是由于钨含量为3.1%的DLC涂层具有优异的膜/基结合力和韧性。
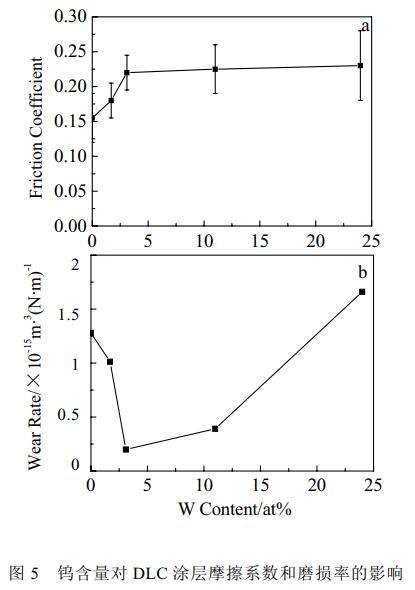
图6为转速为400r/min时载荷对DLC涂层摩擦系数的影响。从图可以看出,低钨含量的DLC涂层的摩擦系数随着载荷的增大先有所增加,但载荷超过之后载荷对摩擦系数的影响较小;高钨含量的DLC涂层在高载荷下的摩擦系数较小。其原因在于:低钨含量的DLC涂层摩擦系数较小,在高载荷下摩擦产生的热量使试样表面的温度达到发生解吸附的温度,DLC涂层表面的解吸附导致对摩副之间的粘着现象更为明显;高钨含量的DLC涂层摩擦系数较大,在高载荷下摩擦表面温度比相同载荷下低摩擦系数的试样摩擦表面温度更高,DLC涂层表面不仅会发生解吸附,还会导致表层的复合涂层发生分解而生成层状石墨结构,表面石墨化对减小摩擦系数的作用更明显;随着DLC涂层摩擦系数和载荷的增加,摩擦表面温升更大,涂层表面石墨化更为显著,因此高钨含量的DLC涂层表现出摩擦系数随着载荷的增加而降低的规律。
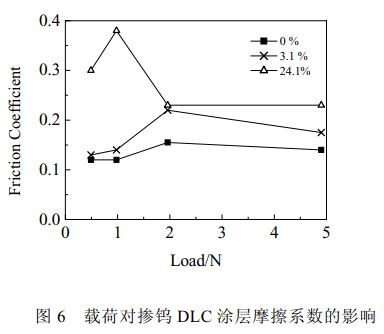
图7为载荷为1.96N时转速对DLC涂层摩擦系数的影响。从图可以看出,转速对纯DLC涂层的摩擦系数影响很小;掺钨DLC涂层在较高转速下的摩擦系数较大。随着转速的增加,摩擦表面温度逐渐升高;纯DLC涂层的摩擦系数较低,最大转速下的摩擦表面温度不足以使DLC涂层表面发生解吸附,试样表面状态在不同转速下基本没有变化,因而摩擦系数变化不大;掺钨DLC涂层的摩擦系数较高,在较高的转速下摩擦表面温度升高导致涂层表层吸附层发生解吸附而引起对摩副之间的粘着作用增强,从而使得摩擦系数增大,由于采用的载荷较低,摩擦力较小,在高转速时的摩擦表面温度仍然低于DLC涂层石墨化的温度,因而没有出现摩擦系数随着转速增加而降低的现象。
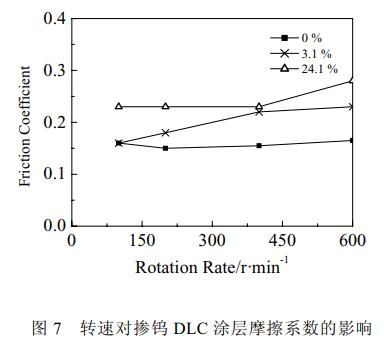
图8为干摩擦条件下掺钨DLC涂层的磨痕形貌。从图可以看出,磨损表面存在一定数量的犁沟,在犁沟内部存在DLC涂层的微观断裂和剥落区域。在摩擦过程中,由于不锈钢基体硬度较低,Si3N4表面微凸体会压入试样表面而导致DLC涂层与不锈钢基体同时发生塑性变形;在变形过程中DLC涂层断裂韧性的不足会引起DLC涂层内部的微观断裂;膜基系统发生变形时会在膜/基界面产生剪切应力,如果应力大于膜/基结合力,将会导致涂层的剥落;DLC涂层的微观断裂和剥落是磨损过程中DLC涂层材料的主要去除机制。为了改善涂覆DLC的软质基体样品的耐磨性,需要从两方面着手:一是改善DLC涂层的断裂韧性和膜/基结合力,减轻在相同变形条件下DLC涂层的微观断裂和剥落;另一方面是在更大深度上提高基体的硬度,以减小涂层的变形。在DLC涂层中掺入适量的钨元素可以明显提高DLC涂层的韧性和膜/基结合力,有效减轻磨损过程中DLC涂层的微观断裂和剥落,从而显著改善其耐磨性。
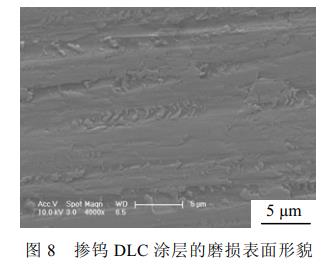
3、结论
1)随着钨含量的增加,DLC涂层的sp3键含量逐渐减小;钨含量到达10%以后,DLC涂层中出现了一定量的WC,且继续增加钨含量对sp3键含量影响不大;摩擦系数随着钨含量的增加而明显增加,钨含量为3.1%的DLC涂层具有最低的磨损率。
2)在干摩擦条件下,低钨含量的DLC涂层摩擦系数随着载荷增加而有所增加,高钨含量的DLC涂层在高载荷下具有较低的摩擦系数;高钨含量的DLC涂层的摩擦系数随着转速的增加而增加,但转速对纯DLC涂层的摩擦系数影响很小。掺钨DLC涂层的磨损主要是由Si3N4球压入试样表面时涂层的微观断裂和剥落引起的。
作者:付志强、王成彪、岳文、彭志坚、于翔、林松盛、代明江
作者:付志强、王成彪、岳文、彭志坚、于翔、林松盛、代明江