关于润滑膜层请看他们怎么说(英文)
2016-08-16

New Challenges for Industrial Tribological Coatings
Allan Matthews
School of Materials, The University of Manchester, United Kingdom
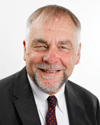
It's All About the Surface - The Role of Tribological Thin Film Coatings in Rolling Element Bearing Applications
Stephen P. Johnson
The Timken Company, North Canton, OH
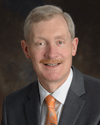