Cr掺杂及Cr过渡层对类金刚石薄膜附着力的影响
2016-11-30
类金刚石薄膜(DLC)由于具有优良的光、电和力学特性,在工业上具有广泛的应用前景。尤其是其具有极低的摩擦因数和耐磨性,近年来DLC膜在切削刀具、自动化机械零部件等表面镀膜涂层处理上已得到了工业应用。但DLC膜的一个致命弱点是内应力很高,导致薄膜附着力差,难以获得较厚薄膜,进而限制了它更广泛的应用范围,如何获得具有良好膜基结合力的DLC涂层已成为DLC涂层领域一个备受关注的关键问题。目前,常见的解决方法主要有:①在DLC膜与基体间设置过渡层,梯度层,(或在沉积过渡层和梯度层的同时,进行离子注入等,这种方法缓解了因膜基界面间的不整合性或热膨胀因数不同而产生的应力。②在DLC中掺杂第三元素,如金属、si、B、N、F等。此类方法中,以金属掺杂DLC膜在应力降低、摩擦性能改善和膜基结合力方面的功效最为突出。
文中旨在研究Cr过渡层以及金属cr掺杂对改善类金刚石薄膜附着力特性的影响,并对其残余应力、摩擦行为等性能进行分析比较,以此来指导DLC薄膜的工程化应用工艺设计。
1、试验方法
1.1薄膜沉积
研究采用线性离子束混合磁控溅射在WC硬质合金、Si基体上沉积了DLC膜,Cr/DLC膜以及Cr-DLC膜。该设备配备有1个38cm长的线性离子束和1个矩形直流磁控溅射靶,在DLC膜沉积时,单独开启线性离子束,通入碳源气体C2H2;沉积Cr/DLC膜时,先进行铬靶溅射,形成Cr应力缓冲层,然后再沉积DLC膜;制备Cr-DLC薄膜时,则同时开启磁控溅射铬靶和线性离子束源进行复合薄膜的沉积。基体样品在丙酮、酒精、去离子水中经过10分钟超声波清洗,热风吹干后放入真空室内。为了提高薄膜与基体的附着力,沉积成膜前对基体进行了10分钟的Ar离子清洗,具体样品沉积参数见表1。
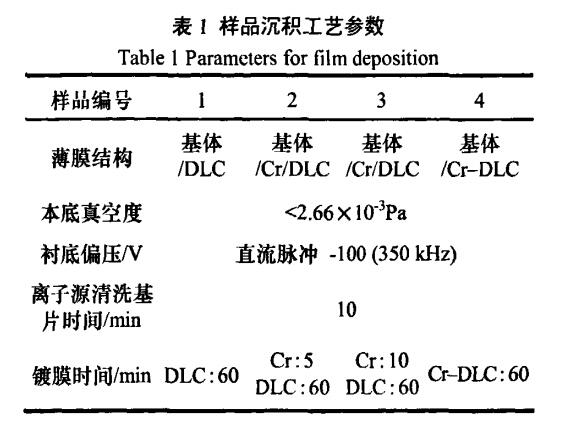
1.2薄膜性能表征
采用Alpha-StepIQ表面轮廓仪测量薄膜厚度,采用JLCST022残余应力仪测量薄膜的残余应力,采用划痕仪WS-2005表征膜基结合力,采用球盘式摩擦磨损试验机(韩国,型号为JLTB-02)对其摩擦性能进行测试。此外,通过荧光显微镜等观察和研究样品经划痕仪测试后的划痕情况。
2、结果与分析
2.1薄膜厚度
采用表面轮廓仪测量1,2,3和4号样品,其膜厚分别为656nm,787nm,904nm,和628nm,其中2和3号样品中,cr过渡层的厚度分别为131nm和246nm。
2.2薄膜的残余应力
图1为测得4个样品的残余应力,从图中可以看出,当DLC薄膜中引入Cr过渡层后,薄膜的残余应力得到了降低,其中当过渡层Cr的厚度约为250nm时,残余应力出现了约50%的明显降低,从3.9GPa降至2.0GPa,而过渡层cr厚度为130nm时,其残余应力变化不大,这说明应力缓冲层具有一个最佳厚度,太薄时,其应力缓冲作用不明显。该组样品中,Crj参杂的DLC薄膜残余应力最低,为0.23GPa。这是因为采用膜基间设置过渡层的方法时,只是缓解了因膜基界面问的不整合性或热膨胀因数不匹配而产生的应力,但是薄膜内部本征应力并没有得到缓解,而根据我们前期的试验结果,在DLC薄膜中掺杂金属cr时,可在薄膜内部形成纳米量级的纳米碳化铬晶体相,这些纳米微粒的出现为DLC薄膜网络结构中的局域应力释放提供了条件,从而导致薄膜生长过程中的本征残余应力极大降低,对外表现为极低的残余应力。
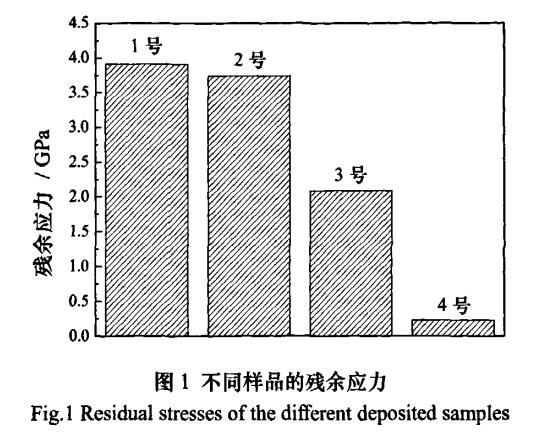
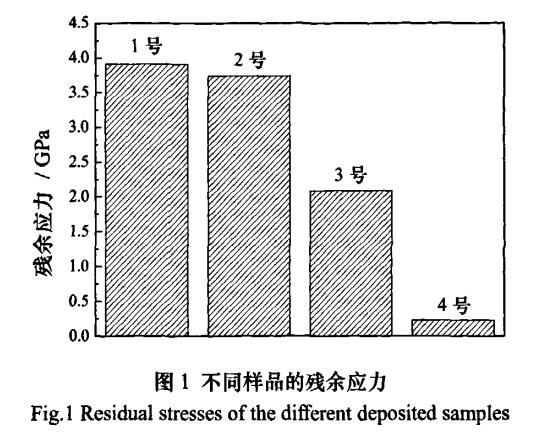
2.3薄膜的膜基结合力
划痕试验法是一种广泛应用于测量硬质薄膜与基体界面结合强度的检验方法,主要是采用一个120度锥角的金刚石压头在薄膜表面上滑动,在此过程中通过自动伺服加载机构持续增加垂直载荷L,当L达到其临界载荷Lc时,薄膜与基体开始剥离,该载荷即为压头完全划透薄膜并使之从其基体上连续剥离所需要的最小载荷,也可理解为薄膜的膜基结合力值。文中,划痕测试采用的最大载荷为70N、加载速度为70N/min、划痕长度为5mm条件进行。

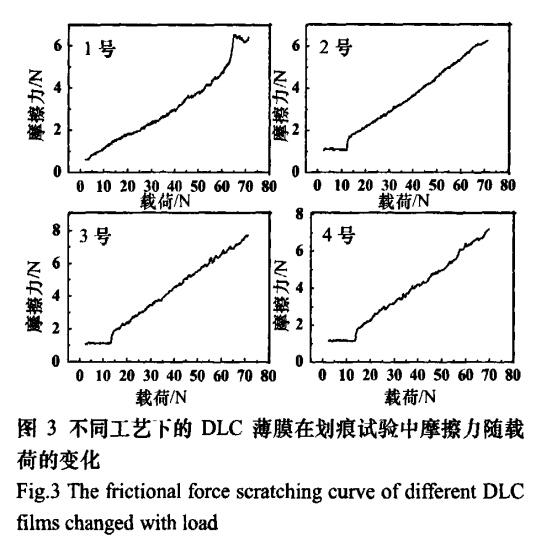

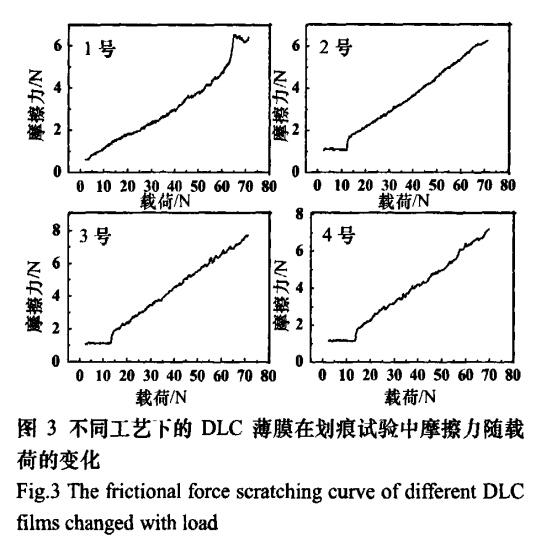
从图2划痕形貌来看,1和4号工艺沉积的薄膜划痕较宽,发生了明显的剥离,其中l号薄膜为鱼鳞状剥离失效,薄膜几乎全部剥落,4号样品则为片状的局域剥落。而2和3号样品无明显的剥落现象,只是在薄膜沿划痕两边形成整齐排列的小裂纹,呈鱼骨状,显示出良好的膜基结合力。
在划痕试验的测试中,加载过程中声信号均无明显的变化,于是仅给出划痕测试过程中的摩擦力变化曲线,如图3所示。对照于划痕形貌,可以得出,1号样品的临界载荷约20N左右,而2号、3号样品均无薄膜剥落现象,基本判断其结合力高于70N,4号样品的临界载荷为45N左右。
根据划痕试验的结果,在增加不同厚度cr过渡层以及进行金属铬掺杂之后,DLC薄膜的结合力均有不同程度的提高,过渡层可以大幅提高膜基结合力,主要是因为在界面处生成了较薄的过渡结合层,能够跟基体进行良好化学键结合,充分缓解了DLC薄膜与基体问因热膨胀因数不匹配而引起的内应力,从而提高了结合力。而金属Cr的掺杂,虽然极大地降低了薄膜的残余应力,一定程度上提高了薄膜与WC硬质合金的膜基结合力,但由于在界面层缺少强有力的化学键合过渡层,所以表现出的膜基结合力仍低于Cr过渡层时的膜基结合力。
2.4薄膜的摩擦学性能
采用球盘式摩擦磨损试验机对制得的薄膜进行摩擦性能的表征,摩擦副为SUJ-2轴承钢,载荷为3N,转速为60mm/s,摩擦距离为100m,薄膜的摩擦因数随摩擦距离变化的动态曲线如图4所示。可以看出,纯DLC薄膜的平均摩擦因数约为0.18左右;以Cr过渡层设计的DLC薄膜均表现出较稳定的低摩擦因数,2号和3号样品的平均摩擦因数分别为0.15和0.14左右,其中Cr过渡层约为250nm时的2号样品的摩擦因数最低;Cr掺杂的DLC薄膜相对摩擦因数较高,且不平稳,约在0.2左右,这一定程度上可归因于Cr-DLC薄膜中形成的碳化铬硬质相具有比纯DLC薄膜更高的摩擦因数所导致的。
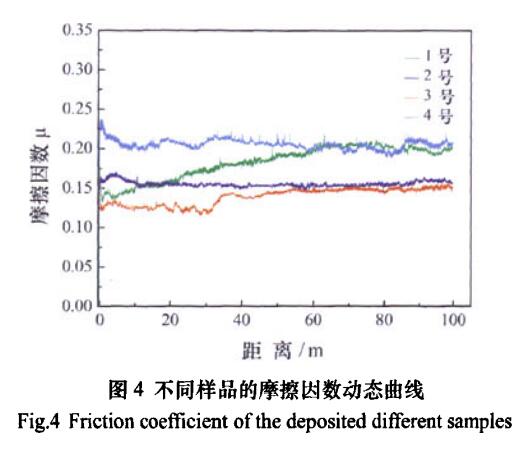
综上,金属Cr过渡层的采用可极大程度地提高DLC薄膜与WC硬质合金问的膜基结合力,同时在过渡层厚度相对优化的情况下,还可以降低其残余应力和摩擦因数,使得薄膜具有更优异的耐磨减摩性能。而金属Cr掺杂则能显著地降低薄膜的残余应力,但因形成的硬质碳化铬相,使得其摩擦行为改善不大。以此相关结果为依据,可预期,通过合理设计DLC薄膜的结构,如厚度优化的过渡层+金属掺杂的DLC薄膜+DLC的薄膜结构,应能获得膜基结合力好、残余应力低、摩擦因数低的优异特性DLC薄膜。
3、结论
(1)通过线性离子束混合磁控溅射沉积设备成功制备了纯DLC、含Cr过渡层以及金属Cr掺杂的DLC薄膜,且过渡层以及金属掺杂结构的采用,使得薄膜的摩擦性能以及膜基结合力都有了较大的改善。
(2)添加的cr过渡层在厚度为250nm时,薄膜的残余应力及结合力的提高较为显著,而金属Cr掺杂的DLC薄膜则能极大的降低薄膜残余应力,因此设计金属过渡层+金属掺杂的DLC+纯DLC的薄膜多层结构应能获得良好综合性能的耐磨、减摩DLC薄膜。
DLC涂层设备请点这里>>
DLC涂层设备请点这里>>