DLC类金刚石表面涂层技术在模具中的应用
发布时间:2018-01-30
1、引言
DLC(类金刚石)涂层技术是一种应用于冲切工具领域的专业技术。DLC涂层的工业化生产开始于20世纪末。与应用于模具上的硬质涂层(如TiN,TiAlN,CrN,TiCN等)相比是一种崭新的涂层技术。在半导体封装、管脚切割和成形制造过程中,高精度的模具是确保产品品质的关键。模具表面质量又决定了产品优良率、生产效率和产品电学性能等。所以,应用于半导体封装行业的模具不但要求高精度,同时也要求模具刃口件向表面低摩擦因数和高硬度的方向发展,而运用等离子体DLC涂层技术的涂层是这一问题的主要解决方案。
2、基本原理
DLC涂层处理使用的是一种物理气相沉积工艺技术PVD(physical vapor deposition)。是在真空条件下(1.3x10-2~1.3x10-4Pa),采用低电压、大电流的电弧放电技术,利用气体放电使靶材蒸发并使被蒸发物质与气体都发生电离,利用电场的加速作用,使被蒸发物质及其反应产物沉积在工件上。
DLC涂层是一种在微观结构上含有金刚石成分的涂层。构成DLC的主要元素为碳,碳原子之间的不同结合方式,最终产生不同的物质:金刚石(diamond)--碳碳以sp3键的形式结合;石墨(graphite)一碳碳以sp2键的形式结合。类金刚石(DLC)一碳碳以sp3和sp2健的形式结合;其涂层结构是由碳的sp3和sp2形态混合而成的无定型组织(没有显性的晶格结构),涂层性能的好坏取决于形成的膜层结构中sp3和sp2各自所占的百分比,sp3所占的比率越高,膜层性能越接近天然金刚石,显微硬度越高;sp2所占的比率越高,膜层的自润滑性能越好,摩擦因数越小,但显微硬度会降低(它和金属之间的摩擦因数的范围一般是0.05~O.2)。通过设定生产流程中的工艺参数和选择不同的靶材,可以控制最终成形膜层的属性来满足不同场合的需求。
3、工艺流程及参数
DLC处理的工艺流程包括所需处理工件基体的处理(抛光、清洗)、靶材的选择、成形工艺条件的设定、成形及成形后的检测等。
要想得到高品质的DLC涂层,工件基体处理的好坏至关重要。将工件要抛光到小于Ra0.2um,涂覆处理后的工件才可得到满意的表面质量,这对成形一些具有光学性能要求的零件是非常重要的(如成形光学镜头和成形LED零件)。这里要注意的是基体表面处理不能留有死角,这关系到膜层是否能与基体牢固地结合。
将要涂覆的工件还要充分清洗。清洗工艺取决于涂覆的质量水平、母材和几何形状。工件装在设定的夹具上,夹具是在使腔体装载尺寸最优化和保证涂覆均匀的基础上设计的。真空室抽真空至10-6托(高真空)来排除系统中的任何污染物。真空室中通入惰性气体并使其离子化。导致产生辉光放电(等离子体)。这是气体清洗阶段并使零件做好最初的金属沉淀准备。
在靶材(用于沉淀的固体金属)上加载高电流、低电压电弧,金属被蒸发并且瞬间离子化,这些金属离子在高能量的作用下通过惰性气体或活性气体进入腔体并沉淀在工件上。在金属沉淀过程中蒸发了的金属(靶材)保持不变。在激活的沉淀过程中,改变气体的体积或种类将会改变膜层的性质,形成像碳化物、氮化物或氧化物的陶瓷。同样,通过改变靶材的材质也可以产生不同的膜层。表1是不同的膜层所用的工艺参数。
在涂覆完成后,还需要对成形后工件的膜层质量进行检测,包括工件的光泽、膜层的厚度是否均匀而且尺寸在控制范围之内,以及膜层是否出现分层现象等。
如果成形后的膜层出现光泽不均匀、有花纹现象,则有可能是靶材的材质的纯净度不够,含有较多的杂质所致。另外还有一种可能性是涂覆设备出现了问题,没有稳定的工艺环境。出现这种情况,首先要排查是否设备出现了问题,如果不是则必须更换靶材。在设备稳定的情况下,膜层的厚度取决于成形的工艺时间.出现膜层厚度超差一般都是处理时间过长或过短所致,只要调整处理时间就可以解决问题。
一般最常见也是比较难解决的的问题是膜层和工件基体之间的结合力不强。出现分层现象(见图3)。出现这种问题的原因有很多种,最主要的有工件清洗得不干净、不彻底,工件的基体没有抛光到工艺要求或者存在缺陷,成形工艺参数不合理等。出现这种情况要一项项去排除,直至找到真正的原因。为了解决基体与膜层分层的问题,有时还需要对工件进行预处理,即在工件上预先涂覆一层金属来消除基体本身的缺陷。
表1膜层种类及工艺参数
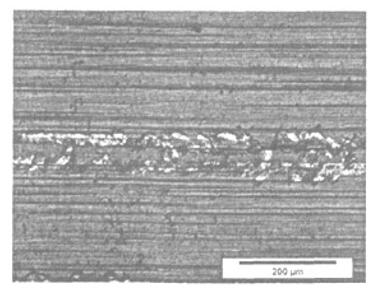
图3 膜层与基体出现分层现象
名称 | 成分 | 膜层厚度/um | 硬度/HV | 摩擦因数 | 最高工作温度/℃ | 处理温度/℃ |
C10 | DLC(ta-C) | 0.5~2.5 | 5000~9000 | 0.1 | 400 | 204 |
C11 | DLC(a-C:H) | 1.0~4.0 | 2000~3000 | 0.1 | 350 | 204 |
C12 | Me-DLC | 1.0~5.0 | 1000~2000 | 0.1 | 350 | 160 |
C14 | C-DLC | 1.0~3.0 | 2200~4000 | 0.06~0.15 | 350 | 180 |
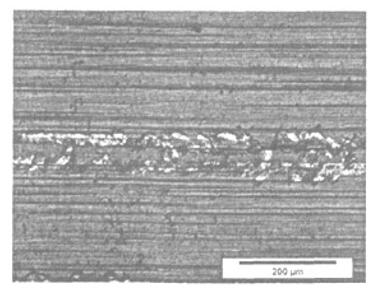
图3 膜层与基体出现分层现象
4、典型应用
DLC涂层以其特有的优势应用于对摩擦和磨损有特殊要求的场合,典型应用以下几个领域。
(1)切削领域:钻头、铣刀、硬质合金刀片等。
(2)金属材料成形领域:凸模、凹模、精密冲裁、压印成形零件等。
(3)模压成形领域:模腔和型芯、顶杆及各类镶件等。
(4)引擎领域:阀类、活塞销、顶杆、活塞等。
(5)半导体领域:引脚成形模具的刀口件、封装模具的成形镶件和镶块等。
(6)其他零部件:轴类、齿轮、轴承、凸轮和从动滚轮等。
在半导体封装模具领域中,由于绿色环保树脂的广泛应用使得成形后产品的脱模越来越困难。在传统工艺加工的模具中,经常出现由于脱模困难而造成产品的报废,相对应需要洗模的周期也越来越短,产品的优良率和生产效率也越来越低,模压工序中生产成本的居高不下成为半导体后道生产中的瓶颈。而使用DLC涂覆工艺处理的模具可以很好地解决这一问题,通过对模具中关键零件(型腔和型芯)的表面涂覆一层DLC涂层,可以大大降低产品脱模力,杜绝因脱模力太大而造成产品报废的现象。同时,生产效率也得到了极大的提高,以前生产不到100模就需要洗模,现在生产1000模以上才需要洗模。
在半导体产品的引脚成形模具中,DLC涂层同样得到了广泛的应用。由于对产品质量要求的不断提高和PPF框架的逐步推广使用,引脚成形时的表面损伤越来越成为关注的焦点,引脚表面在成形时的损伤不但会影响产品的电性能参数,降低产品的使用寿命,而且容易引起产品管脚的虚焊,造成整块电路板的报废。在传统模具中,人们不得不花费大量的时间和精力从数量众多的产品中剔除那些因为引脚损伤而不合格的产品,同时,成形模具的维护、清洗也极为频繁,一般几个小时就要清洗一次,对生产效率造成了极大影响。DLC涂层由于其极低的摩擦因数和自润滑性能而能极大改善这一现象。通过在模具成形零件上涂覆一层DLC涂层。可以有效提高产品的品质、减少维护时间、降低产品的生产成本。
5、结束语
DLC涂层技术是新兴发展起来的一种表面涂覆处理技术,以其优异的高硬度、低摩擦因数和自润滑性能而被用于对摩擦和磨损有特殊要求的场合。其在模具刃口件和成形零件中的应用,可以有效提高模具本身的使用性能,提升产品的品质,明显地增加模具的使用寿命、减少维护时间,从而提高了生产效率,降低了单位生产成本。随着产品品质要求的不断提高和对产品单位成本的严格控制,DLC表面涂覆技术会在模具工业中得到越来越广泛的应用。
声明:本站部分图片、文章来源于网络,版权归原作者所有,如有侵权,请点击这里联系本站删除。
返回列表 | 分享给朋友: |