超硬刀具材料的发展与应用
发布时间:2017-01-09
随着各种新型工件材料及涂层的应用和发展,传统刀具材料,如高速钢、硬质合金、陶瓷等常不能满足难加工材料的加工需求,天然和人造单晶金刚石(PCD)、立方氮化硼(CBN)和聚晶立方氮化硼(PCBN)等超硬刀具材料因具有很高的高温硬度、耐磨性和热化学稳定性,为高硬度材料的切削加工提供了最基本的前提条件,并且在生产中取得了明显效益。本文主要阐述了超硬刀具材料(PCD和PCBN)的发展、性能特点及应用。
1、超硬刀具材料的发展及研究现状
人们用天然金刚石制作刀具已有千年以上历史,人们掌握了人工合成单晶金刚石和金刚石粉的技术并将其制成聚晶金刚石(PCD),又发明了化学气相沉积方法(CVD)制成了金刚石涂层及膜片并使其成为刀具材料。目前,国际上著名的人造金刚石复合片生产商主要有英国的DeBeers公司、美国的GE公司、日本的住友电工株式会社等。PCD刀具的应用范围已由初期的车削加工向钻削、铣削加工扩展。日本UNION公司和旭DIAMOND公司合作开发了金刚石涂层硬质合金立铣刀,其耐磨性是公司原有产品的20倍。金刚石复合片合成技术也得到了较大发展,DeBeers公司已推出了直径为74mm、层厚为0.3mm的聚晶金刚石复合片。国内PCD刀具市场随着刀具技术水平的发展也不断扩大。目前中国第一汽车集团已有100多个PCD车刀试用点,许多人造地板企业也采用PCD刀具进行木制品加工。PCD刀具的应用进一步推动了对其设计与制造技术的研究。PCD刀具的加工范围已从传统的金属切削加工扩展到石材加工、木材加工、金属基复合材料、玻璃、工程陶瓷等材料的加工。PCBN是在20世纪70年代末期紧随着PCD发展起来的一种用于加工硬质铁合金的材料。其具有良好的抗化学腐蚀性,且在高达1200的温度下表现出很好的热稳定性,因此,在刀具尖端的相对高温不会对它产生任何不利的影响,相反还能在切削硬质铁合金时起到加速切削的作用;同磨削相比,使用PCBN无论在技术上还是在经济上都更为有效。在大多数情形下,PCBN表现出比传统的刀具材料如WC和陶瓷更优良的性能。
2、超硬刀具材料的性能特点
1)较高的硬度和耐磨性
金刚石刀具具有硬度高、抗压强度高、导热性好和耐磨性好等特性,可在高速切削中获得很高的加工精度和加工效率。由于聚晶金刚石(PCD)的结构是取向不一的细晶粒金刚石烧结体,虽然加入了结合剂,其硬度及耐磨性仍低于单晶金刚石。表1给出了各种刀具的硬度值,PCD的硬度可达8000HV,为硬质合金的8~12倍;CBN晶体结构与金刚石类似,因此具有与金刚石相近的硬度和强度;CBN微粉的显微硬度为8000~9000HV,其烧结体PCBN的硬度一般为3000~5000HV。
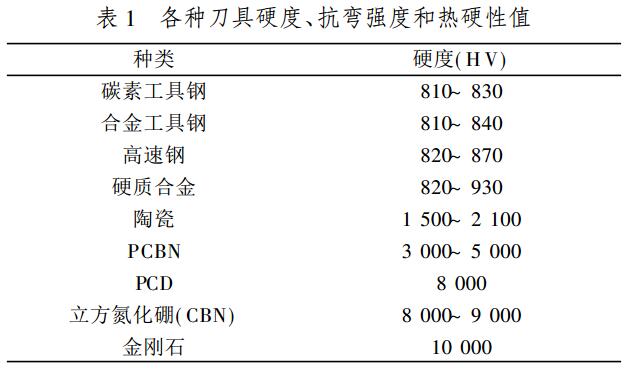
根据材料的耐磨性和强度,给出了各种刀具材料排序的结果,如图1所示。可以看出,金刚石尤其是以纯单晶形式存在的金刚石耐磨性最高。但是由于它具有解理面,在受冲击时往往会表现出脆性,容易被破坏,在所有材料中强度最低。PCBN表现出比传统的刀具材料如陶瓷更优良的性能,其耐磨性仅次于金刚石材料,强度同陶瓷接近,但耐磨性比PCD要差。PCBN在切削耐磨材料中耐磨性分别为硬质合金刀具的50倍,涂层硬质合金刀具的30倍,陶瓷刀具的25倍。
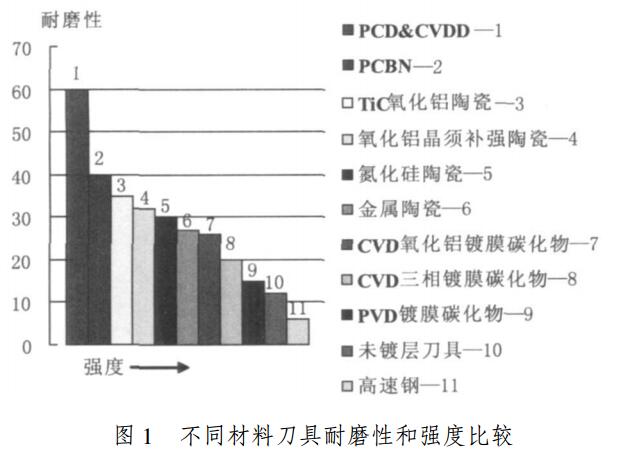
2)较好的导热性
在各类刀具材料中,金刚石的导热性最高,PCD的导热系数为700W/mK,为硬质合金的1.5~9倍,甚至高于PCBN和铜,因此PCD刀具传递热量迅速;CBN的导热性仅次于金刚石,是紫铜的3.2倍,是硬质合金的20倍,立方氮化硼与陶瓷的导热系数比率为37.1,热扩散率比值为65.5,而且随着温度的升高,PCBN的导热系数是增加的,而氧化铝的系数是降低的,PCBN刀具导热系数高,可使刀尖处温度降低,减小刀具的磨损,有利于加工精度的提高[5]。
3)较好的化学稳定性
由于碳对铁有亲和作用,特别在高温下,金刚石能同铁发生化学反应,因此金刚石通常不适合用来机加工铁及其合金工件,很大程度上制约了金刚石的应用。CBN的化学惰性特别大,在1200~1300时也不与铁系材料发生化学反应,与碳在2000才发生化学反应;在中性、还原性的气体中,对酸、碱都是稳定的,其对各种材料的粘结、扩散作用比硬质合金小得多,因此PCBN刀具特别适合加工钢铁材料。
4)较低的摩擦因数PCD和CBN与不同材料间的摩擦因数一般仅为0.1~0.3(硬质合金的摩擦因数为0.4~1),随着切削速度的提高,摩擦因数是减小的。因此超硬刀具可显著减小切削力、减小切削变形、提高加工表面质量。
5)较好的热稳定性PCD的热膨胀系数为0.9*10.6~1.18*10.6,仅相当于硬质合金的1/5,因此PCD刀具热变形小,加工精度高;PCBN在800时的硬度还高于陶瓷和硬质合金的常温硬度,可用比硬质合金刀具高3~5倍的速度高速切削高温合金和淬硬钢。
3、超硬刀具材料的应用
超硬刀具材料可应用于汽车工业、航天航空、机械制造业,实现高速、高效切削。通过近年来PCD刀具的应用分析,PCD刀具主要应用于以下2个方面:
1)难加工有色金属材料的加工。用普通刀具加工,往往产生刀具磨损、效率低等缺陷,而PCD刀具则可表现出良好的加工性能,而且可以实现铸、锻毛坯件的高速、高效加工,一次性完成粗、精磨削,尤其适用于成形、仿形及定尺寸的精密磨削,可使磨削质量和磨削效率得到数倍乃至数十倍的提高;
2)难加工非金属材料的加工。PCD刀具非常适合对石材、硬质碳、碳纤维增强塑料(CFRP)、人造板材等难加工非金属材料的加工。硬质合金硬度高、耐磨性强,用超硬材料代替传统碳化硅和刚玉磨料加工硬质合金工件,可防止工件表面烧伤、微裂纹、缺口或变质层过深等缺陷,提高加工效率和节约磨削成本。通过分析,CBN和PCBN刀具的应用表现在下面几个方面:
1)硬态加工,以车代磨。PCBN刀具具有极高的硬度及红硬性,可获得良好的表面粗糙度,采用PCBN刀具车削淬硬钢可实现以车代磨。如汽车、摩托车齿轮孔的加工,材料多为20CrMnTi,渗碳淬火,硬度为60~62HRC,精度IT6,表面粗糙度0.8m。传统工艺为:机加工->热处理->磨削。采用超硬刀具以车代磨的工艺为:粗加工->热处理->精加工。磨削工艺每班仅能加工100个小齿轮,而新工艺采用PCBN刀具车削,每班能加工400个小齿轮;
2)高速切削,高稳定性加工。在汽车发动机生产线上,灰铸铁缸体的缸孔精加工是关键工序之一,要求缸孔加工尺寸精度高、表面粗糙度值小、稳定性好;由于生产线加工节拍快,所以要求切削速度高,刀具寿命长。采用PCBN刀具即可实现发动机缸孔的高速切削及高稳定性加工。其典型切削参数为:V=500m/min;进给量f=0.2~0.4mm/r;吃刀深度ap=0.2~0.7mm;加工表面粗糙度Ra<=1.6um;刀具寿命>1000件;
3)干式切削,清洁化加工。采用PCBN刀具加工含硼铸铁缸套,切削参数V=200m/min;f=0.1mm/r;ap=0.2~1mm;加工表面粗糙度Ra<=1.6um,精度IT6,二次刃磨间刀具寿命>100件,可实现以车代磨。由于采用干式切削,避免了切(磨)削液及砂轮灰对环境的污染,切屑可回收再利用,符合清洁化生产要求。
4、结语
目前,超硬刀具因其良好的加工质量在制造业得到了有效的应用。随着刀具理论研究的日益深入及其应用技术的进一步推广,PCD和PCBN刀具在超硬刀具领域的地位将日益重要,其应用范围也将进一步拓展。可以预期,超硬刀具的应用范围将迅速扩大。
声明:本站部分图片、文章来源于网络,版权归原作者所有,如有侵权,请点击这里联系本站删除。
返回列表 | 分享给朋友: |
- 上一篇:塑料模具基材上磁控溅射铝膜附着力研究…
- 下一篇:工模刀具的PVD涂层技术解析