切削刀具多弧离子镀膜的应用研究
发布时间:2017-02-04
物理气象沉积的主要方法有真空镀膜、磁控溅射镀膜、多弧等离子体镀膜、离子镀膜分子束外延镀膜等方法。目前PVD技术不仅可沉积金属膜、合金膜,还可沉积化合物、陶瓷、半导体、聚合物膜等。工业发达国家使用PVD涂层工具的比例已超过90%。国内机械加工刀具及精密模具运用涂层的比例分别小于20%和5%。因此,研究适合我国刀具的涂层技术是非常有意义的。目前硬质涂层技术的发展具有以下趋势:为了满足刀具综合力学性能的要求,涂层成分趋于多元化、复合化;为满足不同的要求,涂层成分将更为复杂、更具针对性;在复合涂层中,各单一成分涂层的厚度将越来越薄并逐步趋于纳米化;某些特殊要求的PVD涂层工艺温度将越来越低。
用多弧离子镀膜的方法在高速钢立铣刀上镀纳米复合TiN/AlSiN膜,这项技术已经成功运用到一些刀具企业,取得了良好的社会效益和经济效益。
1、多弧离子镀膜
在PVD技术的应用中,目前在涂镀刀具、模具等镀硬质功能膜方面应用较广泛的涂镀方法之一就是多弧离子镀技术(Arcionplating,AIP)。该技术主要借助于惰性气体(如:Ne,Ar等)的辉光放电作用,使粉末/块状(通常为靶材)材料离化,在带负电荷的基体或者工件上形成薄膜。多弧离子镀膜所用设备点击这里。
1.1工作原理
阴极靶材由镀膜材料制成,接电源负极,镀膜室接地作阳极,电源电压工作区间0~220V,电流工作区间20~100A。基片(即工件)与腔体之间存在负偏压,其取值范围为50~1000V。在10-3~10-4Pa真空条件下点燃真空电弧,阴极靶材表面上出现一些不连续、大小和形状多样、明亮的斑点,它们在阴极表面迅速且不规则地游动,一些斑点熄灭时又有些斑点在其他部位形成,维持电弧的燃烧。接通电源同时使引弧电极与阴极瞬间接触并离开,在引弧电极离开的瞬间,由于导电面积的迅速缩小,电阻增大,局部区域温度迅速升高,致使靶材表面熔化,形成爆发性的金属蒸发,在阴极表面形成局部的高温区,产生等离子体,将电弧引燃,低压大电流的电源维持弧光放电的持续进行。
阴极弧斑的尺寸极小,相关资料测定为1~100μm;电流密度很高,可达105~107A/cm2。每个弧斑存在时间很短,其爆发性地蒸发靶材离子和电子,由于电场的作用在阴极表面附近,金属离子形成了空间电荷,又形成了新的弧斑产生条件,众多的弧斑持续产生,保持了电弧总电流的稳定。阴极弧斑的运动方向和速度受磁场的控制,适当的磁场强度可以实现阴极靶表面均匀刻蚀。
1.2镀膜的工艺参数
影响薄膜质量的因素多而复杂,因此研究工艺参数与薄膜性能指标之间的关系,以实现薄膜性能及工艺优化设计,始终是致力研究的目标。国内外研究表明多弧离子镀的主要工艺参数有:基体沉积温度、反应气体压强与流量、靶源电流、基体负偏压等。
(1)膜沉积温度。膜沉积温度对薄膜生成、生长及性能有着直接影响。一般来说,基体沉积温度高,有利于薄膜的生长,也有利于膜基结合力的提升。但温度过高,会在提高镀膜成本、增加能耗的同时,引起被镀工件晶粒粗大,造成强度和硬度下降等缺陷。
(2)反应气体压强与流量。反应气体的压强与流量大小直接关系到膜层的化学成分、组织结构及性能。毛延发等人在W18Cr4VC05高速钢基体上采用多弧离子镀技术制备了AlSiN镀层,结果表明,随N2分压的增加,薄膜中颗粒和熔滴的密度、直径减小。实验表明,随着氮流量的增加,不但液滴的尺寸会缩小,而且薄膜表面的液滴密度也会大大降低,从而降低薄膜表面粗糙度。
(3)靶源电流。弧斑的数目与靶源电流成正比,较多的弧斑可以增加靶材刻蚀的稳定性。有研究表明在一定的靶源电流范围内,薄膜厚度随靶源电流的升高而增加。但靶源电流过高,会因整体温度的提升而使液滴随之增多,而且液滴的尺寸也会增大,从而影响涂层表面质量和粗糙度。
(4)基体负偏压。基体负偏压是多弧离子镀在镀层时的一个重要参数。基体负偏压在镀膜前预轰击时,可以清除工件表面吸附的气体和污染物。基体负偏压对TiN/AlSiN薄膜性能产生较大的影响,研究结果表明,薄膜表面液滴的密度和直径随基体负偏压的增加而减少,薄膜的显微硬度在一定范围内随着负偏压的增加而增加,薄膜的沉积效率随着偏压的升高先提高后降低。
2、TiN/AlSiN膜在高速钢立铣刀上的应用实验
金属切削刀具需要高硬度、高耐磨性、耐高温性能及耐腐蚀性能。PVD技术可以针对钻头、铣刀、车刀、螺纹铣刀、铰刀及滚齿铣刀等进行镀膜,从而大大提高刀具的使用寿命。本研究选择了比较常用的高速钢(W18Cr4V)立铣刀进行涂镀实验。
2.1 TiN/AlSiN纳米复合涂层中硅和铝对膜性能的影响
研究表明,在TiN/AlSiN涂层中,硅和铝会使膜的晶格常数和晶粒尺寸变小。另外,硅和铝增加会诱发六方相的生长。硅和铝的加入会影响到膜的硬度、摩擦性能、热稳定性等。
(1)硅元素对膜性能的影响。硅含量的变化会对涂层的硬度产生影响。添加少量的硅会使镀膜硬度增加,当硅含量增加到一定值时,膜的硬度达到最大,硅含量超过某个值时,则膜的硬度急剧下降。加入少量的硅可以形成TiAlSiN固溶体,固溶强化和晶格畸变造成的应力增加会造成膜的硬度急剧增大,硅会在膜中形成非晶态的Si3N4。由于nc-TiAlN镶嵌于非晶态的Si3N4的内部而形成nc-TiAlN/a-Si3N4纳米复合结构,抑制膜的晶粒长大,而细晶引起的Hall-Patch效应使得膜的硬度增大。而当硅元素量增加到一定程度后,非晶态的Si3N4引起的TiAlN晶粒分离超过一个最佳值,使得晶界的阻断位错运动作用下降。晶粒细化也能使得膜的界面能增加,从而导致整个体系的能量增高,促使膜向其稳定相h-AlN转化来降低能量,而膜中的六方相h-AlN的致密度和强度明显低于立方相,从而导致膜硬度的降低。Si含量对TiN/AlSiN涂层硬度的影响如图2所示。
另外,硅的加入提高了膜高温下组织的热稳定性、热硬性和抗氧化性,适应于高速切削条件下对膜层的苛刻要求。因此,硅作为膜层的第4元素加入,很大程度上提高了膜的硬度(见表1),改善了韧性、摩擦系数和高温抗氧化性等,所以,纳米复合涂层代表了国际上新一代刀具涂层发展的方向。
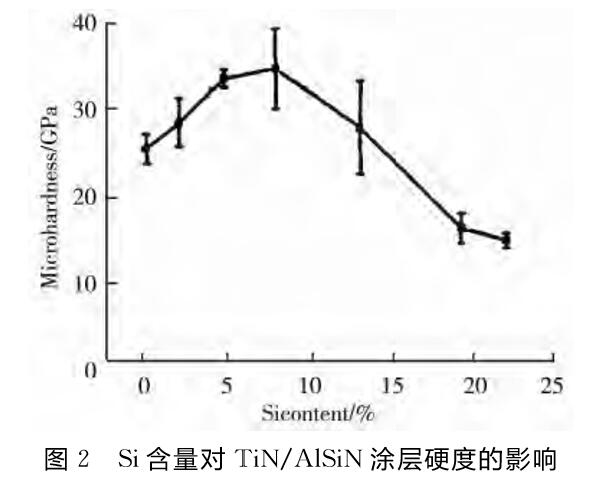
(2)铝元素对膜性能的影响。不同铝含量TiN/AlSiN薄膜在10N载荷下和WC对磨球分别在RT、500℃下测试的摩擦系数-时间曲线如图3所示。T0试样为不含铝的TiCN膜,A1试样含少量铝,A2试样含铝量比A1试样高。从图3中可以看出,不同铝含量的TiN/AlSiN薄膜摩擦系数曲线表现出不同的变化趋势,且不同摩擦学试验温度下表现出的趋势也不同。磨损曲线有磨合阶段、稳定阶段,随温度的升高磨合期也会相应变长,这个过程会发生复杂的物理化学反应。常温下的磨损试验曲线如图3a所示,加入铝元素提高了薄膜的摩擦系数,A1试样铝含量增加摩擦系数也相应增大。TiCN薄膜室温摩擦系数稳定在0.11,所以,TiCN是非常优良的常温润滑膜。从图3b中可以看出,当温度达到600℃时,TiCN润滑膜在经历一段稳定期后,随着薄膜中碳元素的流失(在高温和磨损压应力共同作用下,薄膜中的碳元素会与空气中的氧气发生反应),摩擦系数突然升高。而薄膜中含有较高铝元素的A2试样薄膜在磨合期时铝元素优先与空气中的氧气发生反应,避免了碳元素的流失,同时产生的氧化铝也起到了润滑作用,从而使摩擦系数下降;A1试样的磨合期发生了复杂的物理化学反应,由于铝含量较低,未能完全防止碳的流失,在氧化铝的减磨作用和碳流失的增磨作用的综合效果下,曲线出现了很大的波动。A1试样和A2试样薄膜由于氧化铝的润滑作用,摩擦系数都比T0低,所以,当薄膜工作在高温下时,TiN/AlSiN薄膜就显示出了其高温稳定性的优越性。

2.2实验结果及分析
(1)硬度测试。硬度是硬质薄膜最重要的性能之一。只有在较高硬度的条件下,薄膜才能有效减小磨损,起到强化衬底表面的作用。本实验主要通过纳米压痕仪测试纳米硬度,纳米压痕仪可以解决显微硬度计对薄膜硬度测量误差问题。各类涂层的硬度及热稳定性比较如表1所示。从表1可以看出,TiN/AlSiN超晶格涂层与传统的TiN及TiAlN涂层的硬度相比,硬度和热稳定性都得到大幅度提高。
表1 各类涂层的硬度及热稳定性比较
涂层种类 | 硬度/GPa | 涂层种类 | 硬度/GPa | 涂层种类 | 硬度/GPa |
TiN | 20 | TiCN | 35 | TiN/AlSiN 纳米复合涂层 | 52 |
(2)摩擦性能测试。TiN/AlSiN膜在600℃摩擦性能测试结果如图4所示。左图是600℃摩擦磨损试验的SEM形貌图。右图是600℃在摩擦轨道上的能谱图。从图4可以看出,在600℃高温下,磨削成分里出现了氧元素,之前有报道说氧化物对薄膜有自润滑作用,这也解释了为什么TiN/AlSiN膜在常温下的摩擦系数要比TiCN高,而在高温下却表现出优异的摩擦学性能。
(3)膜-基结合力测试。要发挥膜层的性能,膜和基体的结合力高是前提条件。膜和基体结合力低会导致刀具在使用时发生膜层崩裂和脱落现象。因此我们采用洛氏硬度压痕法测试膜-基结合力。用洛氏硬度计加载1470N,卸载后用100倍光学显微镜观察,观察到的图像如图5所示。从图5可以看出,压痕边缘只有一些细微的裂纹,没有剥落现象,结合强度级别在HF1级,结合力比较强。这是因为薄膜结构是由晶体和非晶体构成,非晶体的存在可以使薄膜通过塑性变形有效释放由外力所产生的应力,因此,薄膜的韧性增强,出现裂纹的几率大大下降。
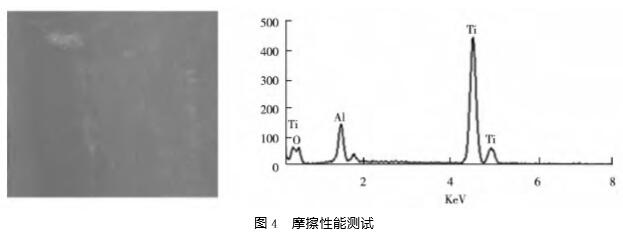
(4)镀膜厚度测试。纳米硬质膜是由两种或两种以上成份或结构不同的薄膜在垂直于薄膜一维方向上交替生长而形成的多层结构。对于两种不同成分或结构组成的多层薄膜,每相邻两层形成一个单元,其厚度称为调制周期。调制周期λ=8nm的纳米多层结构组成,TiN层和AlSiN层,其平均厚度分别为5.8nm和2.2nm。这种共格界面对超晶格涂层的高硬度、高耐磨性、耐高温性能有着重要作用。并且可以根据不同刀具的不同要求,通过调制溅射能量和弧流大小、沉积距离等关键工艺参数,可以灵活准确地调整和控制两相的调制比和涂层厚度。
在高速钢立铣刀表面镀膜的膜层厚度,我们用球坑法结合金相显微镜经过计算得出,约为3μm左右。
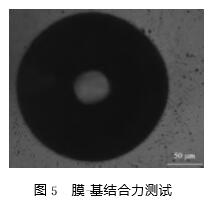
(5)铸铁切削实验。分别用Φ10的高速钢无镀膜立铣刀、Φ10的高速钢镀TiCN膜立铣刀以及Φ10的高速钢镀TiN/AlSiN纳米复合涂层膜立铣刀进行了切削铸铁(加工顶平面)的切削实验。实验表明,如果用无涂镀的高速钢刀具加工铸铁,在一定的转速下(1500n/min、47m/min)的进给速度切削铸铁可以使用3h,而涂镀TiN/AlSiN涂层的刀具则可以使用9h以上。
(6)45钢切削实验。切削45钢(加工侧面)的切削实验,我们分别用10的高速钢无镀膜立铣刀、Φ10的高速钢镀TiCN膜立铣刀以及Φ10的高速钢镀TiN/AlSiN纳米复合涂层膜立铣刀进行了切削加工45钢侧面,都用715n/min的转速及22m/min的进给速度,无涂层的高速钢刀具只能用30min,而涂镀了TiN/AlSiN涂层的刀具则使用3h。涂镀了TiN/AlSiN涂层的高速钢刀具比不涂镀的高速钢刀具切削寿命提高1~6倍。和镀TiCN高速钢立铣刀相比,纳米复合涂层TiN/AlSiN涂镀的高速钢刀具的寿命也有比较明显的提高。这是因为TiN/AlSiN涂是复合膜,TiN层作为AlSiN层的支撑层,形成了比较合理的硬度、组织成分、结合力的匹配。另外,由于Si和Al的加入进一步提高了膜的硬度、高温硬度和抗氧化性,从而进一步提高了切削刀具的使用寿命。
3、结论
相对于单层膜来说,TiN/AlSiN纳米复合涂层形成了硬度、组织成分和结合力的有效匹配,在高速切削的金属切削刀具比较成功的应用。而在复合膜层中,由于加入了铝和硅,提高了刀具的硬度、耐磨性、高温硬度、抗氧化性等,更加适应高速切削刀具。但硅的加入要适当,超过一定量就会引起硬度的下降,也会影响膜和基体的结合牢固度。因此,纳米复合涂层TiN/AlSiNi用于金属切削刀具有广阔的应用空间和良好的发展前景。
声明:本站部分图片、文章来源于网络,版权归原作者所有,如有侵权,请点击这里联系本站删除。
返回列表 | 分享给朋友: |