电弧离子镀TiAlN、TiAlSiN涂层在高温及变温环境中的摩擦学性能
发布时间:2017-12-01
引言
因TiAlN涂层在高温环境中表面可生成致密的Al2O3保护性薄膜,使其在800℃以上的空气中仍然拥有良好的抗氧化性能。因此,从上世纪90年代就开始取代TiN涂层,被广泛应用于切削刀具及机械零部件的保护性涂层方面。但是在更高的温度环境下,涂层因发生相转变,而使涂层的力学性能下降。近些年,研究者们向TiAlN体系中引入Si元素,一方面发现Si元素可以有效降低晶粒尺寸;另一方面,Si元素可以与N原子结合生成Si3N4非晶相,包裹在面心立方TiAlN纳米晶周围,使得TiAlSiN涂层在高温下具有更好的抗氧化性与机械性能。因此,研究TiAlSiN涂层在高温环境中的摩擦行为和磨损机理对其实际应用至关重要。
TiAlN和TiAlSiN涂层在常温及高温条件下的摩擦学性能已经被广泛研究。Fuentes等采用阴极电弧蒸发镀制备了TiAlSiN涂层,研究其在室温、200、400和600℃温度条件下的摩擦学性能,发现在200℃以上的温度条件中,涂层发生了摩擦化学反应,生成的产物起到了润滑保护作用,涂层的耐磨性较室温大大提高。He等通过复合物理气相沉积技术制备了TiAlSiN涂层,并进一步研究了涂层在800℃温度条件下的摩擦学性能。发现涂层在800℃条件下仍然具有较好的耐磨性,高温条件下磨痕区域生成的TiO2起到了主要的润滑保护作用。
但是,这些涂层在实际使用过程中,温度往往是变化的。而目前国内外对变温环境中TiAlN、TiAlSiN涂层的摩擦学性能研究尚未见报到。文中采用电弧离子镀技术制备TiAlN、TiAlSiN涂层,研究其在RT、300℃、600℃的恒温条件下及RT~600℃和600→300℃变温环境中的摩擦学性能,探讨Si元素的添加对TiAlN涂层在高温及变温环境的摩擦学性能的影响。
1、试验
1.1、涂层制备
试验使用沈阳北宇真空设备厂生产的电弧离子镀系统。选用2mm×20mm×30mm的AISI304(成分如表1所示)不锈钢板材作为基材,首先使用砂纸对其表面进行打磨,然后进行镜面抛光处理,抛光后的基材放入无水酒精中清洗10min,然后热风吹干待用。分别选用Ti50Al50(a/%)合金靶和Ti30Al60Si10(a/%)合金靶,在Ar/N2气氛中制备TiAlN和TiAlSiN涂层。真空室本底真空度约为5×10−3Pa。基材悬挂在真空室内的圆形旋转挂具上,转速为13r/min。镀膜前,在真空室中通入Ar至5Pa,在基材偏压−900V的条件下,离子清洗5min。镀膜工艺参数为:基体偏压−580V,占空比25%,基材到靶面的距离15cm,弧源电流40A,工作气压维持在1.3Pa左右(流量比Ar∶N2=2∶3),时间90min,沉积温度250℃。
AISI304不锈钢的化学成分
AISI304不锈钢的化学成分
Element | C | Mn | P | S |
Content | ≤0.08 | ≤2.00 | ≤0.045 | ≤0.030 |
Eelment | Si | Cr | Ni | |
Content | ≤1.00 | 18.0−20.0 | 8.0−10.5 |
1.2、摩擦学性能测试
使用兰州中科凯华生产的HT-1000型球盘式摩擦磨损试验机测试涂层的摩擦学性能,摩擦副选用直径为5mm的氧化铝球。摩擦磨损试验条件为:旋转半径3mm、转速196r/min、时间20min、载荷2.2N。使用TR200型表面粗糙度仪测量磨痕的截面轮廓。根据公式(1)计算涂层的磨损率:
$w=V/SF$
其中V磨损体积,S滑行总距离,F载荷。RT~600℃升温试验中,样品周围环境温度在20min内,从室温匀速升至600℃;在600→300℃降温试验中,温度从600℃度开始自然冷却,20min后样品周围环境温度约为300℃。
涂层的硬度采用HV-1000Z型显微硬度计测量。测试条件为:加载时间10s、载荷50g。
1.3、组织结构表征
使用荷兰PHILIPS公司XPERT-PRO-MRD-A25型X射线衍射仪(XRD)进行涂层的物相分析,选用Cu靶Kα射线(λ=0.154nm)。
2、结果与讨论
2.1、涂层成分
涂层的EDS检测结果如表2所示。两种涂层的表面都检测出了少量的O元素,有可能是因为涂层在放置的过程中,表面少量未被N化的Ti或Al被氧化;也有可能是因为在镀膜过程中,真空室内壁释放的少量O参与了成膜。
TiAlN和TiAlSiN涂层的EDS成分
Coatings | Ti | Al | Si | N | O |
TiAlN | 24.45 | 23.77 | 47.54 | 4.24 | |
TiAlSiN | 14.58 | 32.81 | 3.17 | 46.82 | 2.61 |
2.2、涂层表面与截面形貌
图1(a)为TiAlN涂层的表面形貌,可以发现表面存在一部分较大的融滴颗粒,颗粒尺寸范围约为1~8μm,从图1(c)涂层的截面形貌可以看出涂层厚度约为8.0μm。图1(b)为TiAlSiN涂层的表面形貌,表面的融滴颗粒数量相对较少,颗粒尺寸约1~5μm,涂层的厚度约为8.5μm(图1(d))。以上两种涂层表面的颗粒主要来自于阴极靶表面“弧斑”区域的熔池。
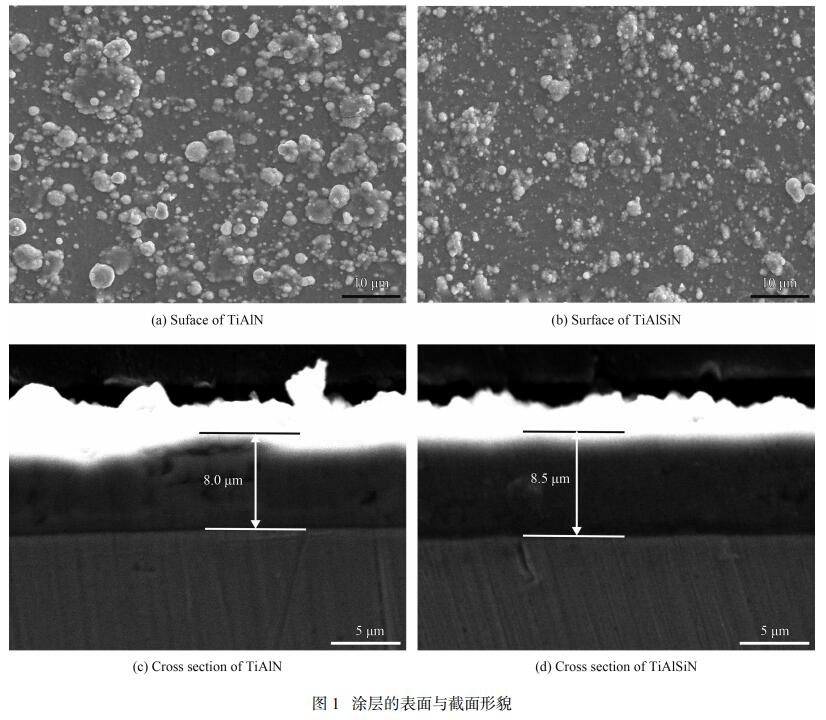
2.3、涂层物相分析
图2为TiAlN和TiAlSiN涂层的XRD图谱。涂层的衍射峰位对应于面心立方TiAlN和面心立方α-Fe。其中,电弧离子镀制备的TiAlN涂层呈现(220)择优取向。与TiAlN涂层相比,TiAlSiN涂层呈(200)择优取向,衍射峰强度下降,宽度变宽。原因有可能是因为Si原子的加入,使涂层的晶粒细化[7]。涂层衍射峰位中未出现Si3N4对应的衍射峰,可能是因为Si3N4以非晶相存在。试验结果同D.Philippona等[7]在–100V基体偏压制备的Si原子数分数为6%(EDS)涂层的XRD衍射峰位非常相似。
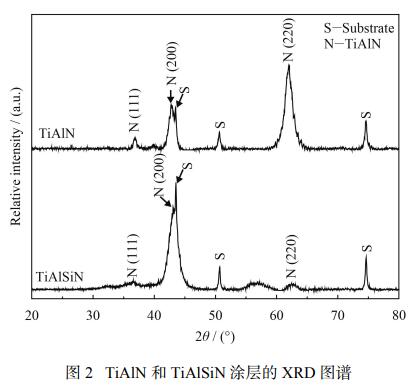
2.4、涂层的硬度
图3为TiAlN和TiAlSiN涂层显微硬度。TiAlN涂层的硬度值为1631HV0.05。与TiAlN涂层相比,TiAlSiN涂层的硬度有所升高,这主要是因为Si元素的加入使涂层的晶粒得到细化所致。
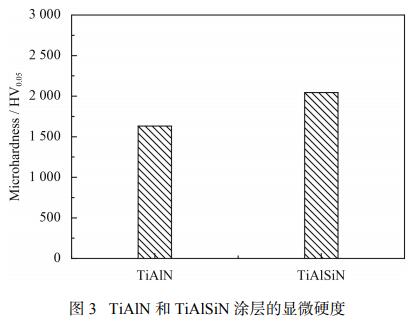
2.5、TiAlN涂层在高温及变温条件下的摩擦学性能
2.5.1、RT、300℃、600℃恒温条件下
图4为TiAlN涂层在室温、300℃、600℃条件下的摩擦因数。可以看出涂层在室温条件下的摩擦因数相对稳定,摩擦因数值总体稳定在0.8左右。在300℃条件下,涂层的摩擦因数在前6min的“磨合阶段”持续上升,摩擦因数值稳定在1.4左右约3min后开始突然下降,并伴随较大的波动。在600℃条件下,摩擦因数值最低而且相对较平稳,波动较小。
图5为TiAlN涂层在RT、300℃、600℃条件下的磨痕形貌。表3为相应温度条件下磨痕内外的EDS结果。从图5可以看出,在室温条件下磨痕的边缘出现了较多的小裂纹,说明接触区域涂层在摩擦副交变应力的作用下,局部发生轻微疲劳断裂。涂层剥落的小颗粒和摩擦副的共同作用使磨痕表面产生了明显的“犁痕”。磨痕区域中,小颗粒与摩擦副的实际接触面积要远大于单位面积的涂层,这导致了小颗粒内部聚集着较大的能量[16],继而与空气中水分子和氧气反应生成了氧化物颗粒,并且粘附在磨痕区域涂层表面,反过来对涂层又起到了一定的保护作用。涂层的磨损机理主要是疲劳断裂和磨粒磨损。
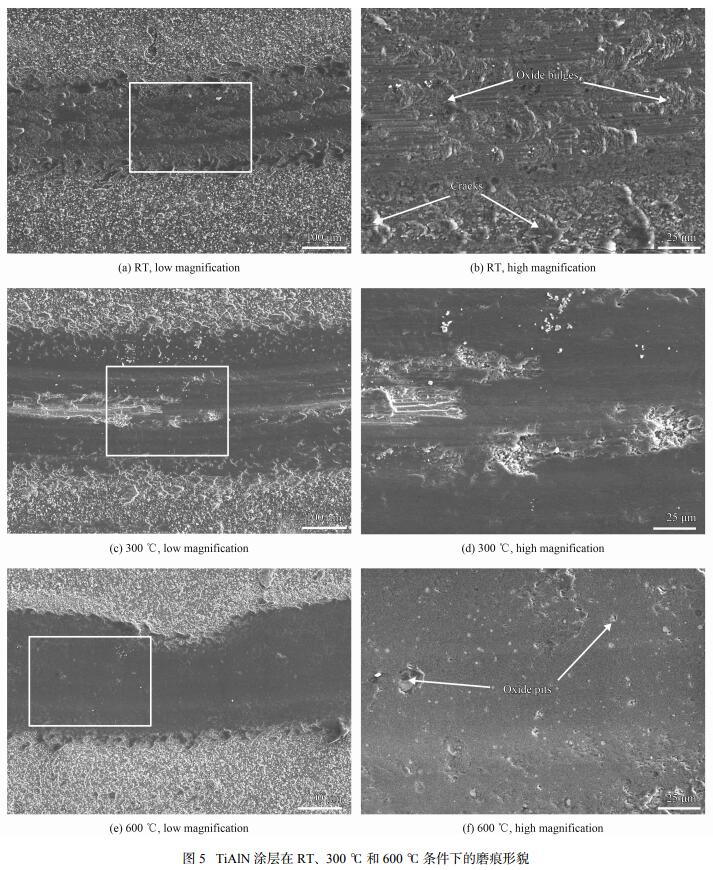
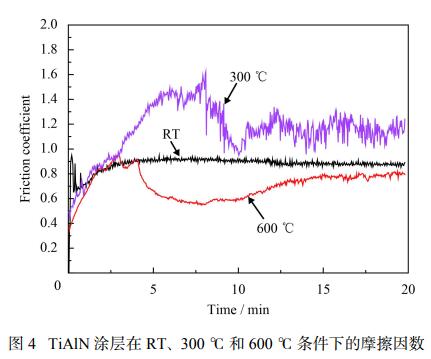
图5为TiAlN涂层在RT、300℃、600℃条件下的磨痕形貌。表3为相应温度条件下磨痕内外的EDS结果。从图5可以看出,在室温条件下磨痕的边缘出现了较多的小裂纹,说明接触区域涂层在摩擦副交变应力的作用下,局部发生轻微疲劳断裂。涂层剥落的小颗粒和摩擦副的共同作用使磨痕表面产生了明显的“犁痕”。磨痕区域中,小颗粒与摩擦副的实际接触面积要远大于单位面积的涂层,这导致了小颗粒内部聚集着较大的能量[16],继而与空气中水分子和氧气反应生成了氧化物颗粒,并且粘附在磨痕区域涂层表面,反过来对涂层又起到了一定的保护作用。涂层的磨损机理主要是疲劳断裂和磨粒磨损。
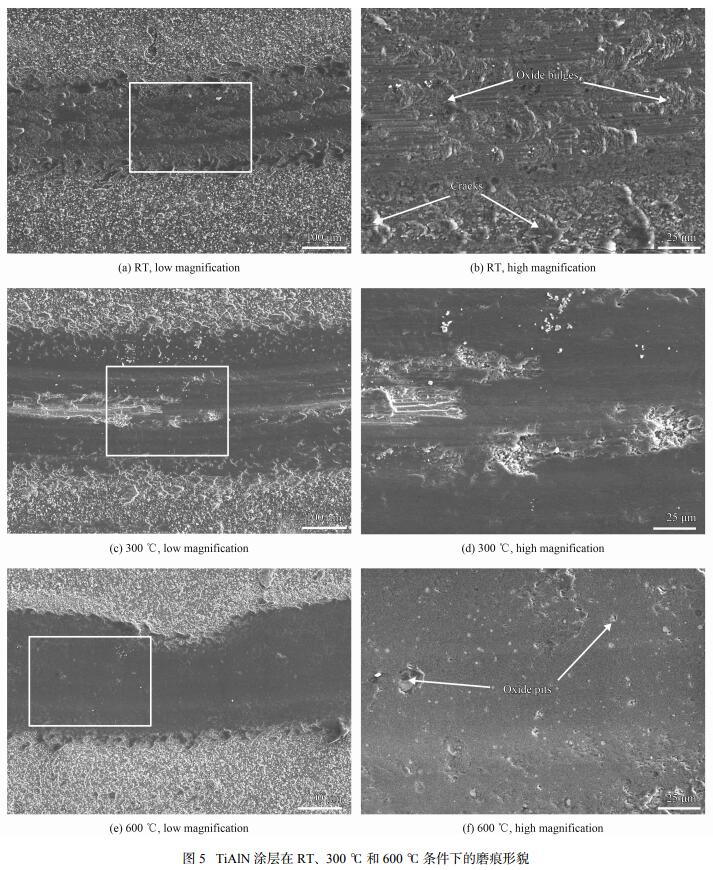
TiAIN涂层在RT、300 ℃和600 ℃条件下磨痕内外EDS分析结果
T/℃ | Position | Ti | Al | N | Fe | Cr | O |
RT | Inside | 20.12 | 18.69 | 34.29 | 0.19 | 0.06 | 26.64 |
Outside | 25.83 | 21.87 | 48.33 | 0.4 | 0.17 | 3.39 | |
300 | Inside | 17.54 | 16.79 | 29.79 | 2.08 | 0.65 | 33.15 |
Outside | 23.0 | 21.41 | 50.84 | 0.4 | 0.12 | 4.22 | |
600 | Inside | 21.69 | 20.81 | 42.9 | 0.33 | 0.07 | 14.20 |
Outside | 23.36 | 21.59 | 48.45 | 0.41 | 6.19 |
300℃条件下,涂层的磨痕宽度变大。同时,可以发现磨痕表面有粘着磨损的迹象,涂层成块脱落,磨损较严重,局部已经磨穿。这可能是因为在300℃的环境中,空气湿度迅速下降,粘附在涂层与摩擦副表层的水分子膜受到破坏,而这层膜对摩擦的影响非常大[16],导致摩擦副与涂层直接接触,摩擦较剧烈。一方面,较剧烈的摩擦磨损导致Al2O3小球的磨斑面积增大,使磨痕变宽;另一方面,导致涂层开始发生较严重的脱落,涂层表面粗糙度升高,导致摩擦因数波动较大。从表3中磨痕区域的能谱结果中可以看出,磨痕区域Fe元素含量(原子数分数)有所升高,这说明涂层已经磨穿。
600℃条件下,涂层的表面较完整。在磨痕区域内,EDS选区分析结果显示磨痕区域生成了许多氧化物凹坑(如图5(f)所示),但是凹坑之外的区域中O含量与磨痕外侧区域中O含量非常接近,都为6%左右,从表3中可以看出,600℃条件下磨痕区域的O元素含量比室温和300℃条件下还要低。这主要是因为600℃条件下,较高的环境温度加上摩擦产生的热量,使磨痕区域发生氧化,而这些氧化反应优先在磨痕微小区域以“点蚀”方式进行。这些细小的氧化物颗粒在摩擦副与涂层之间又起到了一定的润滑作用,保护尚未发生氧化的区域。因此,磨痕表面较完整,摩擦因数值较低。另一方面,Mayrhofer和ChenL等[17-18]在研究温度对TiAlN涂层的机械性能影响时发现,TiAlN涂层会因为亚稳相分离形成紧密的晶粒结构,而出现时效硬化现象。600℃的高温可能在一定程度上促进了磨痕区域涂层内部组织的变化,而使其机械性能改善,对耐磨性的提高也起到一定的帮助。涂层的磨损机理主要为氧化磨损引起的“点蚀”。
2.5.2、RT~600℃和600→300℃的变温环境中
图6为TiAlN涂层在RT~600℃和600→300℃变温环境中的摩擦因数,图7是相应温度的磨痕形貌,表4是相应的EDS分析。
在RT~600℃的升温环境中,涂层的摩擦因数在前8min保持缓慢上升的趋势(如图6所示)。主要是因为随着环境温度缓慢上升,空气湿度逐渐下降。吸附在摩擦副与涂层之间的水分子膜被破坏,涂层磨损逐渐变得剧烈起来。如图7(a)所示,磨痕的宽度较宽,表面出现了剥层。摩擦因数在试验进行11min左右开始出现较大的波动,其原因类似于300℃时的情况,涂层出现了大块的剥落,局部被磨穿,涂层表面粗糙度升高,导致摩擦因数变化加大。
在600→300℃的降温环境中,涂层的摩擦因数比较平稳,平均值在0.5左右。选区的EDS结果显示,图7(d)中磨痕光滑区域O含量很高(约55%),说明在磨痕表面与摩擦副接触区域极有可能生成了钝化膜。600℃恒温条件下,涂层发生了以氧化磨损为主的点蚀,但是在600→300℃的降温环境中,涂层温度下降较快,不足以维持涂层本身的点蚀,导致在摩擦副与涂层之间的润滑颗粒减少,涂层与磨痕的接触面积增大,这为磨痕接触区域生成钝化膜提供了能量条件。对比表4与表3可知,在降温环境中磨痕区域的O含量要大于600℃恒温条件下的O含量。
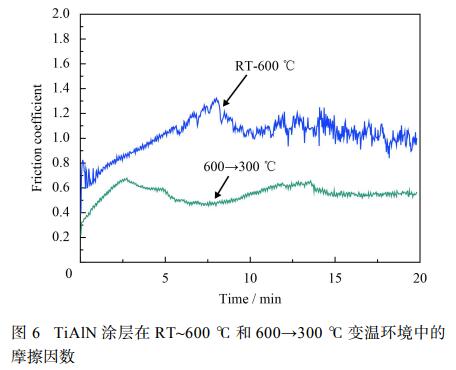
在RT~600℃的升温环境中,涂层的摩擦因数在前8min保持缓慢上升的趋势(如图6所示)。主要是因为随着环境温度缓慢上升,空气湿度逐渐下降。吸附在摩擦副与涂层之间的水分子膜被破坏,涂层磨损逐渐变得剧烈起来。如图7(a)所示,磨痕的宽度较宽,表面出现了剥层。摩擦因数在试验进行11min左右开始出现较大的波动,其原因类似于300℃时的情况,涂层出现了大块的剥落,局部被磨穿,涂层表面粗糙度升高,导致摩擦因数变化加大。
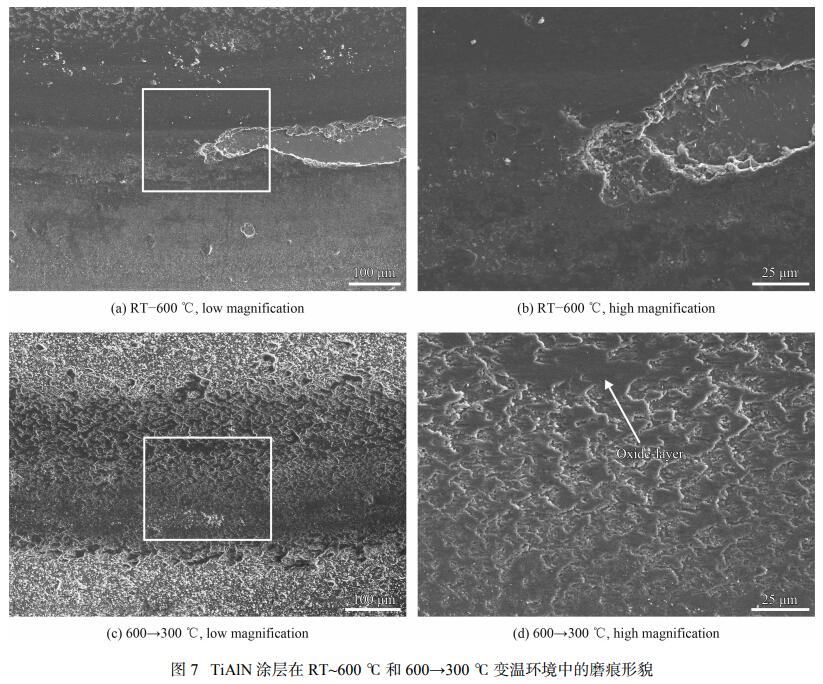
涂层在RT~600 ℃和600→300 ℃变温条件下磨痕内外EDS分析结果
T/℃ | Position | Ti | Al | N | Fe | Cr | O |
RT−600 | Inside | 19.41 | 18.15 | 29.12 | 0.77 | 0.3 | 32.25 |
Outside | 24.43 | 21.81 | 49.76 | 0.38 | 0.16 | 3.46 | |
600→300 | Inside | 17.57 | 16.48 | 25.74 | 0.32 | 0.11 | 39.79 |
Outside | 22.95 | 21.31 | 50.41 | 0.31 | 0.1 | 4.93 |
图8为TiAlN涂层在不同环境温度条件下的磨损率,其中涂层在300℃和RT~600℃条件下已局部磨穿,主要是因为涂层发生了粘着磨损,涂层大块的脱落。在常温下,磨损率最低,因为表面粘附的氧化颗粒对涂层起到了保护作用。600℃条件下因为氧化物颗粒的润滑作用及自身机械性能的提高,导致涂层的磨损率相对较低。在600→300℃的降温环境中,磨痕接触区域生成了钝化膜,对涂层起到了保护作用,其磨损率与600℃恒温条件下相差不大。
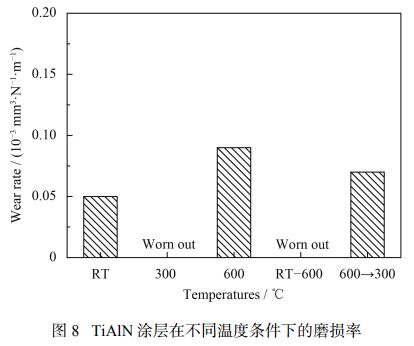
2.6、TiAlSiN涂层在高温及变温条件下的摩擦学性能
2.6.1、RT、300℃、600℃恒温条件下
图9为TiAlSiN涂层在不同恒温条件下的摩擦因数。在室温条件下,涂层摩擦因数平稳,其平均值约为0.85。600℃条件下,涂层的摩擦因数值也较平稳,平均值约为0.75左右。在300℃条件下,磨损比较剧烈,经多次重复试验,确定其在6min左右磨穿。因此,取同样条件下摩擦5min的试样,以分析TiAlSiN在300℃温度环境下的失效原因及磨损机理,可以观察到其摩擦因数在前4min左右快速升高至1.4左右,然后迅速下降。
图10为常温、600℃以及300℃摩擦5min的条件下涂层的磨痕形貌。在室温条件下,涂层的磨痕相对较平整,从高倍磨痕形貌(图10(b))可以看到,在磨痕中间区域,密布着细小并排列整齐的裂纹,成“鱼鳞状”。这说明磨痕中间区域在摩擦副交变应力的作用下,出现了疲劳裂纹,涂层的磨损机理为疲劳磨损。
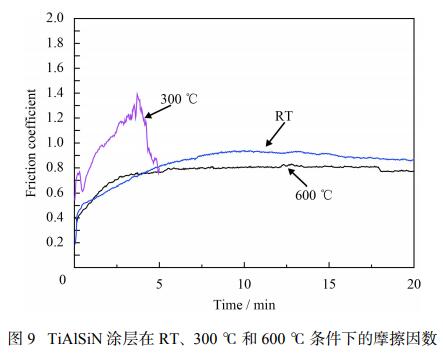
图10为常温、600℃以及300℃摩擦5min的条件下涂层的磨痕形貌。在室温条件下,涂层的磨痕相对较平整,从高倍磨痕形貌(图10(b))可以看到,在磨痕中间区域,密布着细小并排列整齐的裂纹,成“鱼鳞状”。这说明磨痕中间区域在摩擦副交变应力的作用下,出现了疲劳裂纹,涂层的磨损机理为疲劳磨损。
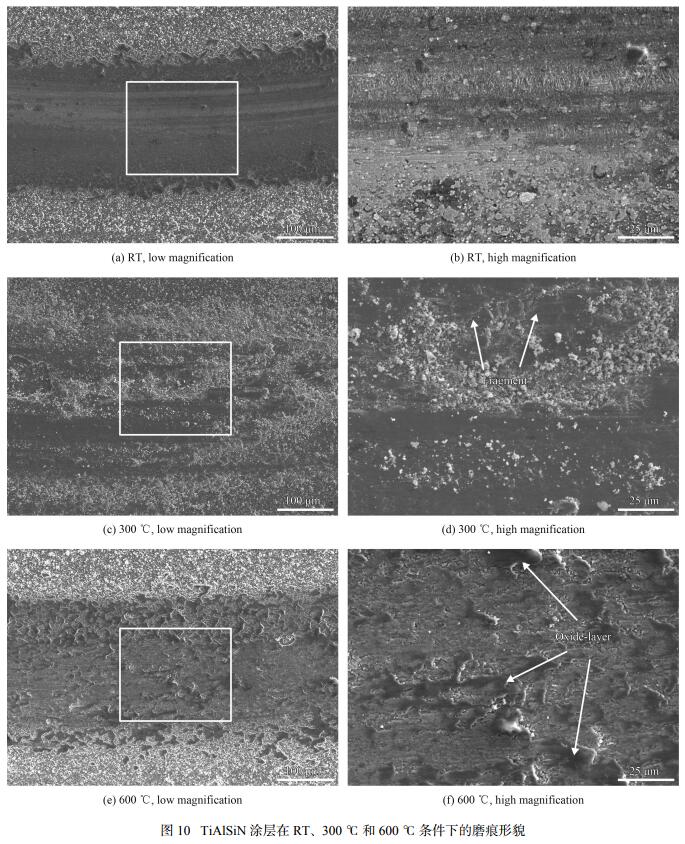
图10(c)(d)中给出了300℃条件下,涂层磨损5min的磨痕形貌。可以发现磨痕区域破损非常严重,在短短5min之内涂层就发生了剥落,表4中磨痕区域EDS结果中Fe含量的升高也说明涂层处在磨穿的临界厚度[15]。其磨损机理与TiAlN涂层在300℃时非常相似,主要是因为300℃条件下空气湿度下降,涂层与摩擦副摩擦剧烈,导致摩擦力增大,摩擦因数升高。而导致300℃条件下,涂层耐磨性低于TiAlN涂层的原因有可能是:TiAlSiN涂层中Al元素含量相对较高,并且加入了Si元素,导致面心立方TiN晶体结构缺陷浓度增加,涂层内部存在着较大不均匀的微观内应力,在摩擦副交变应力的作用下,较TiAlN涂层更容易发生剥落。
600℃条件下,磨痕表面比较完整。从表5中可以发现,磨痕区域O元素的含量比较高,说明此时磨痕区域发生了较明显的氧化。EDS选区分析结果显示,如图10中标注的地方已经生成了氧化层,对涂层起到了保护作用[14]。其磨损机理同TiAlN涂层在600→300℃的降温环境中非常相似,之所以没有发生类似于TiAlN涂层在600℃恒温条件下的“点蚀”,是因为Si元素的添加,以及较高的Al含量提高了涂层的高温抗氧化性。由表5可见,磨痕外部涂层中的O含量同室温状态下相比,并未出现升高,这也说明了TiAlSiN比TiAlN涂层拥有更好的高温抗氧化性。
涂层在RT、300 ℃和600 ℃条件下磨痕内外EDS分析结果
T/℃ | Position | Ti | Al | Si | N | Fe | Cr | O |
RT | Inside | 14.46 | 35.77 | 3.96 | 10.02 | 0.62 | 0.15 | 35.01 |
Outside | 13.98 | 32.63 | 3.17 | 46.82 | 0.59 | 0.19 | 2.61 | |
300 | Inside | 16.49 | 32.75 | 3.48 | 26.69 | 2.6 | 0.64 | 17.33 |
Outside | 16.03 | 32.76 | 3.00 | 44.37 | 0.37 | 0.15 | 3.31 | |
600 | Inside | 16.37 | 37.00 | 4.32 | 1.3 | 0.3 | 0.16 | 40.55 |
Outside | 14.61 | 33.02 | 3.80 | 44.59 | 0.32 | 0.14 | 3.52 |
2.6.2、RT~600℃和600→300℃的变温环境中
图11为TiAlSiN涂层在RT~600℃和600→300℃变温环境中的摩擦因数。如图11所示,在升温过程中,TiAlSiN涂层的摩擦因数在前10min缓慢上升。从图12(a)(b)磨痕形貌中可以发现,涂层有明显的塑性位移及表面“撕裂”现象。这应该是受空气湿度逐渐下降的影响,使磨损变得剧烈。在12min左右,摩擦因数突然降低,其原因是剥落的涂层在磨痕区域碎裂成磨粒,起到了降低摩擦因数的作用。同时,也因为磨痕区域涂层发生大块脱落,致使表面粗糙度增加,导致摩擦因数波动较大。如表6所示,磨痕区域Fe含量增加较明显,说明涂层发生局部磨穿。
在600→300℃的降温环境中,涂层的摩擦因数较平稳,平均值约为0.65左右。涂层的磨痕区域EDS选区分析结果显示,磨痕表面生成了氧化膜,氧化产物(TiO2、Al2O3、SiO2)对涂层都起到一定的润滑保护作用[14]。如表6所示,磨痕区域较高的O元素含量也充分地说明了降温环境中磨痕区域发生了氧化反应。与600℃恒温条件相比,磨痕表面形成了连续的氧化膜,使得在降温阶段摩擦因数值最低。
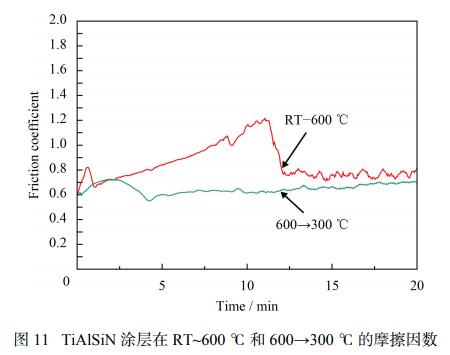
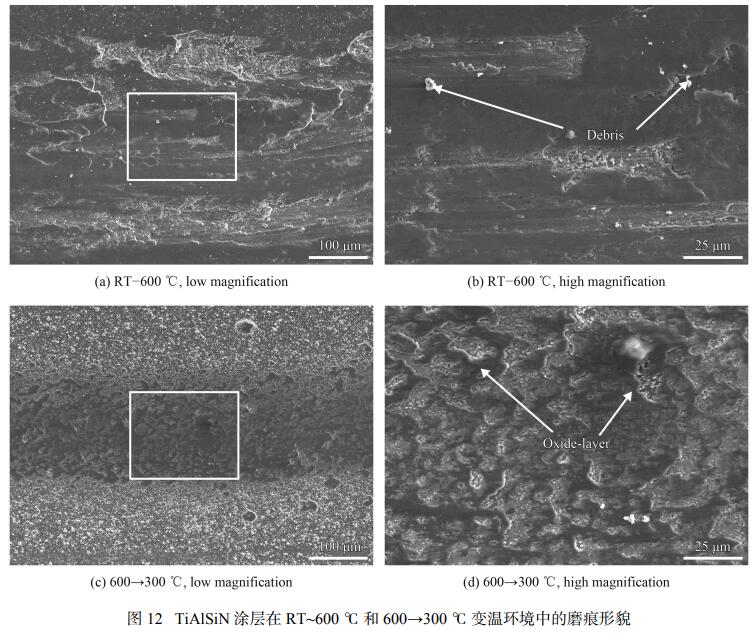
在600→300℃的降温环境中,涂层的摩擦因数较平稳,平均值约为0.65左右。涂层的磨痕区域EDS选区分析结果显示,磨痕表面生成了氧化膜,氧化产物(TiO2、Al2O3、SiO2)对涂层都起到一定的润滑保护作用[14]。如表6所示,磨痕区域较高的O元素含量也充分地说明了降温环境中磨痕区域发生了氧化反应。与600℃恒温条件相比,磨痕表面形成了连续的氧化膜,使得在降温阶段摩擦因数值最低。
涂层在RT~600 ℃和600→300 ℃变温条件下磨痕内外EDS分析结果
T/℃ | Position | Ti | Al | Si | N | Fe | Cr | O |
RT−600 | Inside | 9.62 | 19.84 | 2.07 | 30.3 | 10.12 | 2.71 | 25.33 |
Outside | 15.7 | 34.4 | 3.01 | 43.14 | 0.34 | 0.28 | 3.14 | |
600→300 | Inside | 17.4 | 37.13 | 4.21 | 3.2 | 0.75 | 0.5 | 36.81 |
Outside | 15.84 | 32.6 | 3.33 | 43.67 | 0.53 | 0.09 | 3.94 |
图13为TiAlSiN涂层在不同温度下的磨损率。如图13所示,涂层在600→300℃降温阶段具有较低的磨损率,这主要归因于其表面形成了连续氧化膜。涂层在300℃条件下磨损剧烈,约6min就已经磨穿。He[14]研究TiAlSiN涂层在RT、400、600、800℃条件下的恒温摩擦学性能,其结果与本试验类似。
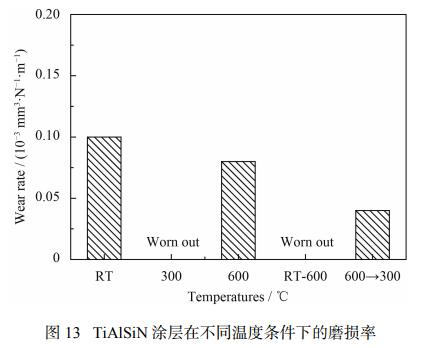
相较于TiAlN涂层,在600℃条件下,TiAlSiN涂层的摩擦因数由0.65增至0.75,磨损率由0.09×10−3mm3/(N·m)降至0.08×10−3mm3/(N·m);在600→300℃的降温环境中,TiAlSiN涂层的摩擦因数由0.5增至0.6,磨损率由0.07×10−3mm3/(N·m)降至0.04×10−3mm3/(N·m)。说明随着Si元素的加入使涂层的抗氧化性增强,磨痕区域生成的氧化物量减少,涂层的摩擦因数相对升高,但是涂层的耐磨性得到一定的改善。
3、结论
(2)TiAlN涂层在室温条件下,磨屑发生了氧化反应粘结在磨痕表面对涂层起到了一定的保护作用。在300℃和RT~600℃的环境中,涂层磨损剧烈,涂层局部磨穿。在600℃条件下,磨痕表面发生了以氧化磨损为主的“点蚀”,生成的氧化产物起到很好的润滑作用,摩擦因数为0.5。在降温环境中,氧化作用较600℃时降低,磨痕表面生成了氧化物膜,对涂层起到了良好的保护和润滑作用,摩擦因数值最低,约为0.7。
(3)TiAlSiN涂层在600℃,较TiAlN涂层抗氧化性增强,磨痕表面生成了致密氧化膜,对涂层起到了保护作用。在600→300℃的降温环境中,涂层表面形成了较连续的氧化膜,对涂层起到了很好的保护和润滑作用,摩擦因数和磨损率最低。
感谢作者:冯长杰, 陈恩
感谢作者:冯长杰, 陈恩
声明:本站部分图片、文章来源于网络,版权归原作者所有,如有侵权,请点击这里联系本站删除。
返回列表 | 分享给朋友: |