PVD制备TiAISiN涂层的研究进展
发布时间:2020-03-02
TiAlN涂层具有较好的抗氧化性和耐磨性,能有效延长刀具的使用寿命。近年来随着高速切削和干式切削技术的发展,对刀具材料的耐磨性、热稳定性及抗氧化性等提出了更高的要求。在高速及干式切削过程中,刀具刃口的温度高于TiAlN涂层的抗氧化与热分解温度,常常导致刀具涂层氧化,硬度急剧下降。TiAlN涂层已无法完全满足高温下的使用要求,新涂层材料的研发迫在眉睫。近年来,许多研究者开始采用在TiAlN涂层中添加合金元素的方法来提高涂层的性能:如B元素可以提高涂层的硬度;Y、Cr元素或者少量的La元素可提高涂层的氧化温度;Zr、V元素可提高涂层的抗磨损能力;Si元素不仅可以改善涂层的硬度与耐磨性,而且能显著提高涂层的热稳定性与抗氧化性。目前,TiAlSiN纳米复合涂层引起了工业界的极大兴趣,被认为是最新一代的超硬涂层材料,并成为国内外学者的重要目标,得到广泛研究。
1、TiAlSiN涂层的微观结构
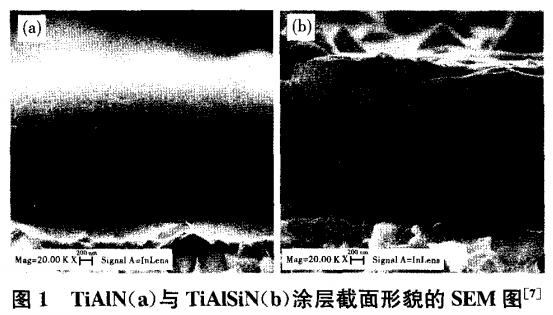
在Si含量较少的TiAlSiN涂层(约为2%,原子分数)中,Al和Si原子置换fcc结构TiN晶格中Ti原子的位置,形成TiAlSiN固溶体,而Al和Si的原子半径小于Ti的原子半径,会引起晶格畸变,使品格常数减小;当Si含量逐渐增多(约为5%,原子分数)时,涂层中出现非晶Si3N4相,形成Si3N4非晶包裹TiAlN纳米晶的复合结构,使涂层晶粒长大受到抑制;当si含量增加到一定值(约为22%,原子分数)时,非晶相Si3N4增多,以致形成纳米晶甚至非晶。受制备方法和工艺的影响,也可能在TiAlSiN涂层中同时形成h-A1N相。
TiAlSiN涂层的晶格常数和晶粒尺寸会随着A1含量的增加而减小,这与Si含量带来的影响相似。另外,研究发现一定含量的Si和Al元素会诱发六方相的生长。喻利花等发现在Si含量为1.29%(原子分数)的涂层中h-TiAlN晶粒有长大现象。M.Parlinska-Wojtan等的研究中指出(Al+Si)含量增加到一定值时,涂层中的fcc_TiAlN物相会分解出现h-A1N物相。Rafaja与YinyuChang等的研究表明,当(A1+Si)与(Ti+Al+Si)的原子比超过0.6时,涂层中的立方结构会向六方结构转变。高的h-A1N含量会导致涂层的硬度急剧下降,因此在涂层的制备过程中,应注意控制(Al+Si)的含量来获得最佳性能的涂层。
2、TiAISiN涂层的力学性能
在TiAlN涂层中,Si含量的变化会对涂层的硬度产生影响。添加少量的Si使TiAlN涂层硬度增加;当Si含量增加到一定值时,涂层的硬度达到最大值;当Si含量继续增加时,涂层硬度发生急剧下降,如图2所示(原子分数)。研究表明,在TiAlN涂层中加入少量Si会形成TiAlSiN固溶体,固溶强化作用和晶格畸变造成的应力增加会引起涂层硬度明显增大,从TiAlN涂层的30GPa左右增加到TiAlSiN涂层的40GPa以上。Si含量增加会在涂层中产生非晶Si3N4相,由于nc-TiAlN镶嵌于非晶态Si3N4的内部而形成nc-TiAlN/a-Si3N4纳米复合结构,抑制涂层晶粒的长大,而细晶引起的Hall-Petch效应致使涂层的硬度增大;此外,细小的TiAlN阻碍位错的运动,也会使硬度增加。但是当Si元素增加到一定量后,非晶Si3N4相引起的TiAlN晶粒分离超过一个最佳值,使晶界的阻断作用失效。另外晶粒细化会使涂层界面能增加,从而导致整个体系的能量升高,促使涂层向其稳定相h-AlN转化来降低能量。而涂层中六方相(h-AlN)的强度和致密度明显低于立方相,因此,也会导致涂层硬度的降低。
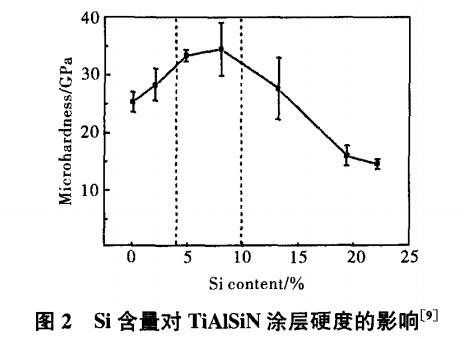
目前关于TiAISiN涂层结合力的研究仍存在着一些争议。DonghaiYu等。采用“空心阴极放电技术+中频磁控溅射技术”的混合PVD方法制备了一系列不同si含量(0~22.14%,原子分数)的TiAlSiN涂层。通过对比发现,添加si元素后涂层的结合力降低,相比而言低si含量的涂层有较好的膜基结合力,且结合力随si含量的增加而降低。而时婧等利用磁过滤电弧离子镀技术在高速钢基体上制备了不同Si含量(O~O.07%,原子分数)的TiAlSiN涂层,无Si加入的TiAlN涂层结合力最高,si含量为0.07%(原子分数)的涂层结合力要高于Si含量为0.04(原子分数)和0.06%(原子分数)的涂层。Si元素的加入使涂层结合力下降的主要原因是TiAlSiN涂层中有较高的残余应力,并且脆性Si3N4相也会使TiAlSiN涂层的结合力降低。膜基结合力除与Si含量有关外,还与基体硬度、涂层厚度、制备工艺等因素有关,因此对于结合力的研究还需进一步深入。
TiAlSiN涂层的摩擦系数随着Si含量的增加而降低。Si元素的引入降低涂层摩擦系数的主要原因与摩擦区域发生的化学反应有关。在TiAlS涂层摩擦实验中,Si3N4与空气中的H2O发生反应,生成SiO2。或者Si(OH)2摩擦层。这种摩擦层可以起到自润滑和保护的作用,有利于涂层在长时间运行下使摩擦系数处于稳定状态。
3、TiAISiN涂层的高温抗氧化性与热稳定性
研究资料表明,TiAlN涂层的耐热及抗氧化温度在800~900℃,超过此温度后,亚稳态的c-TiAlN会向稳态的TiN和h—AlN转化,从而导致涂层失效。而添加Si元素后,涂层的抗氧化温度可提高到1000℃以上。1000℃氧化时,TiAlN涂层硬度急剧下降而TiAlSiN涂层的硬度几乎保持不变,并且TiAlSiN涂层的氧化层厚度仅有TiAlN涂层氧化层厚度的1/2,可见Si元素的添加使涂层的抗氧化性大大提高。在氧化过程中,TiAlN涂层中Al原子向外扩散,O原子向内扩散,在涂层表层形成金红石型TiO2和Al2O3氧化层,而疏松的TiO2氧化层会增加O原子的扩散通道,使涂层进一步被氧化。另外,TiAlN涂层中的柱状晶结构较容易形成裂纹等缺陷,促进O原子向内扩散而迅速造成涂层失效。而TiAlSiN涂层在氧化过程中出现上层富Al下层富Ti的结构,使涂层表面优先生成致密的Al2O3氧化层。另外,Si元素会抑制锐钛矿晶粒的长大,进而阻碍氧化过程中TiO2由锐钛矿向金红石的转变,使涂层抗氧化性得到提高。
TiAlSiN涂层中Al和Si元素的含量也会影响涂层的抗氧化性。M.Pfeiler等研究发现,添加Si元素后涂层的抗氧化性有明显提高,并且Si含量增加使涂层的氧化层厚度也有一定程度的减小,这说明si含量的增加也能提高涂层的抗氧化性。YinyuChang等研究表明,当(Al+Si)与/(Ti+A1+Si)原子比约为O.33时,Ti原子沿着柱状晶结构向外扩散形成TiO2氧化物,当(A1+Si)与(Ti+Al十Si)原子比为0.67和0.72时,涂层晶粒细化,氧化时生成的A12O3氧化层能有效阻碍O原子向内扩散从而阻止涂层继续氧化。
si元素的添加不仅能改善TiAlN涂层的抗氧化性,而且对涂层的高温热稳定性也有一定的影响。有研究发现,在800~1000℃退火,Ti0.28Al0.51Si0.21涂层由h-A1N、c-TiN和非晶相组成,当温度升高至1100℃与1200℃后,涂层中原有的不稳定的h-AlN晶相逐渐消失,表明涂层在1000℃以上具有高的稳定性。Si元素添加提高涂层热稳定性的原因是涂层中形成了nc-TiAlN/a-Si3N4纳米复合结构,而非晶态Si3N4界面相能抑制h-A1N稳定相的形成;同时,非晶态Si3N4可以提供比金属氮化物晶体更高的热稳定性,从而使涂层的热分解温度上升。但另一方面,退火过程中涂层晶粒发生长大,应力得到一定释放,晶界处生成较厚的非晶组织,这些现象会导致涂层硬度降低而削弱涂层的使用性能。
4、TiAlSiN涂层的发展趋势
TiAlSiN涂层具有较高的硬度、优异的高温抗氧化性、良好的热稳定性和耐磨性,已在刀具等行业得到广泛的应用。但目前制备的TiAlSIN涂层仍然存在结合力差、残余应力大等问题。由于涂层的结合强度受基体和涂层的界面影响很大,因此,优化涂层的结构设计及制备工艺,或采用多层化涂层或梯度化涂层都可改善涂层的结合力。如可以通过提高基体负偏压,增强离子轰击作用,使膜基界面形成混合区,减少界面物理性能的突变;或在基体/膜层加入梯度过渡中间层,改善层间化学与物理性能的突变来提高膜基间结合力。另外,对TiAlSiN涂层进行后处理可降低涂层的残余应力,增强刀刃的抗崩刃能力,其机理研究将成为TiAlSiN涂层今后的一个重点研究方向。
声明:本站部分图片、文章来源于网络,版权归原作者所有,如有侵权,请点击这里联系本站删除。
返回列表 | 分享给朋友: |